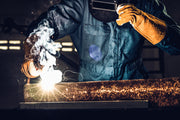
Shielding gases play a pivotal role in modern welding processes, particularly in MIG (Metal Inert Gas) welding and TIG (Tungsten Inert Gas) welding. These gases protect the weld pool from atmospheric contaminants, ensuring high-quality, durable joints. This guide explores the applications, benefits, and best practices for selecting and using shielding gases in MIG welding and TIG welding, empowering welders to optimize their workflows and achieve superior results.
Understanding Shielding Gases in Welding
Shielding gases are inert or semi-inert gases used to prevent oxidation, porosity, and other defects during welding. In MIG and TIG welding, these gases create a stable arc and shield molten metal from oxygen, nitrogen, and hydrogen in the air. Common shielding gases include argon, helium, carbon dioxide (CO2), and gas blends.
MIG Welding Shielding Gases: Applications and Benefits
Primary Gases for MIG Welding
- Argon-CO2 Blends (75/25): Ideal for carbon steel, offering stable arcs and minimal spatter.
- Pure Argon: Used for aluminum and non-ferrous metals.
- Tri-Mix (Argon/Helium/CO2): Enhances penetration in stainless steel welding.
Advantages of MIG Shielding Gases
MIG welding gases improve deposition rates, reduce cleanup time, and enable faster welding speeds. CO2 blends are cost-effective for thick materials, while argon-heavy mixes deliver cleaner welds on thin metals.
TIG Welding Shielding Gases: Precision and Performance
Common TIG Welding Gases
- Pure Argon: Standard choice for most TIG applications, providing excellent arc stability.
- Argon-Helium Mixes: Boost heat input for copper or thick aluminum.
TIG Gas Benefits
TIG shielding gases support precise control over weld aesthetics, critical for aerospace and artistic projects. Helium additions increase travel speeds on conductive metals without compromising quality.
MIG vs. TIG: Gas Selection Criteria
Factor | MIG Welding | TIG Welding |
---|---|---|
Material Thickness | CO2 blends for >1/4" steel | Helium for >3/8" aluminum |
Cost Efficiency | Higher gas consumption | Lower flow rates (10-20 CFH) |
Weld Appearance | Functional finishes | High-precision cosmetic welds |
Best Practices for Optimizing Shielding Gas Use
Flow Rate Calibration
Maintain 20-30 CFH for MIG and 10-20 CFH for TIG welding. Use regulators with built-in flow meters to prevent turbulence.
Gas Lens Technology in TIG
Upgrade to gas lens collets for improved coverage, especially in tight spaces or outdoor environments.
Common Challenges and Solutions
- Porosity: Check for leaks in gas lines.
- Arc Instability: Verify gas purity (>99.95% for TIG).
- Spatter: Adjust CO2 percentage in MIG mixes.
Future Trends in Welding Gas Technology
Emerging developments include AI-powered gas blending systems and eco-friendly synthetic gases that reduce carbon footprints while maintaining performance.
Conclusion
Mastering shielding gas selection for MIG and TIG welding requires understanding material properties, project requirements, and gas behaviors. By implementing the insights and best practices outlined in this guide, welders can significantly enhance productivity, weld quality, and cost-efficiency across diverse applications.
Understanding how each shielding gas performs will help you a lot in your next welding project, and we hope our article was helpful in that.
No matter what kind of welding machine you need, Doughty Welder can provide for your needs. Contact our sales team if you need advice beyond what this article provides. Our team of experts can help you make the right choice.
🧐🧐🧐You might like the following:
2. MIG and MAG Welding - Is There a Difference?
3.Based on 4000+ customer reviews, this plate gold welding artifact stan