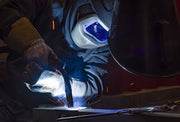
Introduction to MIG and MAG Welding: Understanding the Basics
What Are MIG and MAG Welding?
MIG (Metal Inert Gas) and MAG (Metal Active Gas) welding are two subtypes of gas metal arc welding (GMAW). Both processes use a continuously fed wire electrode and shielding gas to protect the weld pool from atmospheric contamination. While they share similarities, their distinct gas compositions and applications create critical differences.
Historical Context of GMAW Development
The origins of GMAW trace back to the 1940s when industries sought faster welding methods for wartime production. MIG welding emerged first, leveraging inert gases like argon and helium. MAG welding evolved later as manufacturers experimented with reactive gas blends (e.g., CO₂) to improve cost efficiency and weld characteristics on carbon steel.
The Core Difference Between MIG and MAG Welding
Shielding Gas Composition: The Defining Factor
MIG Welding: Inert Gas Dominance
MIG welding relies on inert gases such as:
-
Pure argon (for non-ferrous metals)
-
Argon-helium blends (for aluminum and copper alloys)
-
Argon-hydrogen mixtures (for stainless steel)
These gases do not chemically react with the molten metal, ensuring stable arcs and clean welds.
MAG Welding: Active Gas Blends
MAG welding employs reactive gases like:
-
Carbon dioxide (CO₂)
-
Argon-CO₂ mixtures (e.g., 75% Ar + 25% CO₂)
-
Argon-oxygen blends (e.g., 98% Ar + 2% O₂)
Active gases interact with the weld pool, enhancing penetration and arc stability on ferrous metals.
Technical Breakdown: How MIG and MAG Processes Work
MIG Welding Workflow
-
Equipment Setup: Constant voltage power source, inert gas cylinder, wire feeder.
-
Material Preparation: Clean non-ferrous surfaces (aluminum, magnesium).
-
Welding Execution: Short-circuit or spray transfer modes for thin or thick materials.
-
Post-Processing: Minimal spatter due to inert gas shielding.
MAG Welding Workflow
-
Gas Selection: CO₂ or argon blends tailored to steel grades.
-
Parameter Adjustment: Higher voltage for deeper penetration.
-
Welding Techniques: Globular transfer for heavy plates; pulsed MAG for automotive panels.
-
Slag Management: Slight oxidation requires post-weld brushing.
Material Compatibility: When to Use MIG vs. MAG
MIG Welding Applications
-
Aluminum Fabrication: Aerospace components, marine structures.
-
Stainless Steel: Food processing equipment, architectural features.
-
Copper/Nickel Alloys: HVAC systems, electrical busbars.
MAG Welding Applications
-
Carbon Steel: Structural beams, pipelines, automotive frames.
-
Low-Alloy Steels: Heavy machinery, agricultural implements.
-
Galvanized Steel: Automotive body repairs (with flux-cored wire).
Equipment and Cost Considerations
MIG Welding Setup Costs
-
Inert Gas Expenses: Argon costs ~50 per cylinder (vs. $20 for CO₂).
-
Wire Types: ER4043 aluminum wire (5/lb).
-
Machine Requirements: AC/DC inverters for aluminum ($2,000+).
MAG Welding Economic Advantages
-
Gas Savings: CO₂ is 40-60% cheaper than argon blends.
-
Higher Deposition Rates: 15-20 lbs/hr vs. 8-12 lbs/hr for MIG.
-
Versatile Consumables: Flux-cored wires reduce gas needs in windy conditions.
Performance Comparison: Strengths and Limitations
MIG Welding Pros and Cons
Advantages:
-
Superior weld appearance on aluminum
-
Minimal post-weld cleanup
-
Low hydrogen levels reduce cracking risk
Disadvantages:
-
Limited penetration on thick steel
-
High gas costs for large-scale projects
-
Sensitive to drafts/wind
MAG Welding Pros and Cons
Advantages:
-
Deep penetration for heavy steel
-
Cost-effective for high-volume production
-
Tolerates mild surface contamination
Disadvantages:
-
Increased spatter requiring grinding
-
Not suitable for non-ferrous metals
-
Higher skill requirement for parameter tuning
Industry-Specific Use Cases
Automotive Manufacturing
-
MIG: Aluminum body panels (Tesla Model S), battery trays.
-
MAG: Chassis assembly (Ford F-150), exhaust systems.
Construction and Infrastructure
-
MAG: Structural steel welding (I-beams, bridges).
-
MIG: Stainless steel handrails, architectural cladding.
DIY and Small-Scale Workshops
-
MIG Dominance: Hobbyists prefer MIG for versatility across metals.
-
MAG Limitations: CO₂ tanks require frequent refills for home users.
Common Misconceptions Debunked
Myth 1: "MIG and MAG Machines Are Interchangeable"
Reality: While many GMAW units support both processes, gas delivery systems differ. MIG requires precise argon flowmeters, while MAG setups need CO₂-compatible regulators.
Myth 2: "Active Gases Always Produce Inferior Welds"
Reality: MAG welds on carbon steel often exceed MIG in tensile strength due to deeper fusion zones. AWS D1.1 codes approve MAG for critical structural joints.
Myth 3: "MIG Is Obsolete in Modern Factories"
Data Insight: 68% of U.S. manufacturing plants still use MIG for aluminum work (AWS 2023 report), though MAG dominates steel fabrication.
Future Trends in GMAW Technology
Smart Welding Systems
-
AI-powered parameter optimization (Miller AugmentedArc)
-
Real-time gas flow monitoring via IoT sensors
Environmental Innovations
-
Recycled shielding gas programs (Praxair EcoLine)
-
Low-spatter MAG wires reducing fume extraction needs
FAQs: MIG vs. MAG Welding
Can I Use CO₂ Gas for MIG Welding Aluminum?
No. CO₂ reacts violently with molten aluminum, causing porosity and cracking. Always use 100% argon.
Which Process Offers Faster Travel Speeds?
MAG welding achieves 20-30% higher speeds on steel due to active gas stabilization.
Is Certification Different for MIG/MAG Operators?
Yes. AWS Certified Welder programs have separate performance qualifications for MIG (Module 4) and MAG (Module 5).
Conclusion: Choosing the Right Process
Selecting between MIG and MAG hinges on three factors:
-
Base Material: Non-ferrous → MIG; Steel → MAG
-
Project Scale: Low-volume → MIG; High-output → MAG
-
Budget Constraints: Premium quality → MIG; Cost efficiency → MAG
By aligning gas selection, equipment capabilities, and operational goals, fabricators maximize productivity while meeting ASTM and AWS quality standards.

No matter what kind of welding machine you need, Doughty Welder can provide for your needs. Contact our sales team if you need advice beyond what this article provides. Our team of experts can help you make the right choice.
🧐🧐🧐You might like the following:
1.How to MIG welding aluminum for beginners
2. How To TIG Weld Stainless Steel: A Comprehensive Guide for Beginners
3.Based on 4000+ customer reviews, this plate gold welding artifact stan