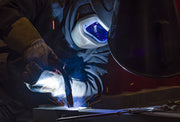
MIG welding ( metal inert gas protective welding ) is a widely used welding technology in the industrial field, favored for its high efficiency, flexibility and ease of operation. However, the excessive splash created during MIG welding is a common problem that not only affects the welding quality but also increases the cleaning cost and time. This article will explore how to reduce MIG welding splash, and provide practical solutions to help industrial users to improve welding efficiency and quality.
1. MIG welding splash cause
Before exploring how to reduce splash, you first need to understand the cause of splash. The MIG welding splash is mainly caused by the following factors:
1. Inappropriate welding parameter setting: incorrect configuration of voltage, current and wire speed may lead to the unstable state of the arc, which then cause splash in the welding process.
2. Lack of gas protection measures: the flow rate setting of the protective gas (such as argon or carbon dioxide) is not enough or the gas purity does not meet the requirements, which may lead to the oxidation reaction of the molten tank, which will also increase the splash phenomenon in the welding process.
3. Quality problems of welding wire: including the use of low quality wire or the presence of impurities (such as oil or rust) on the surface of the wire, which may negatively affect the stability of welding.
4. Improper selection of Angle and speed during welding: the welding torch Angle is not set correctly, or the welding speed is too fast or too slow, which will lead to the increase of splash phenomenon during welding.
5. Problems of welding equipment: aging equipment or poor contact with the grounding wire, which will also adversely affect the welding quality.
2. Practical way to reduce MIG welding splashes
2.1. Optimize the welding parameters(best MIG welder settings for steel)
Voltage and current setting: adjust the voltage and current according to the thickness and type of the welding material. Too high voltage will increase the splash phenomenon, while too low voltage may cause the problem of opaque welding. When using the MIG welder, please refer to the equipment instructions or online resources to find the appropriate parameters.
The wire transmission speed needs to match the current, too fast or too slow will lead to arc instability, increase the splash phenomenon.
2.2. Choose the right protective gas( best gas for MIG welding )
Industrial MIG welding gas mix:In carbon steel welding, a mixed gas of 75% argon gas and 25% carbon dioxide (C25) is often used, which can effectively reduce the splash and improve the welding quality.
Gas flow: Ensure that the gas flow is moderate (usually 20-25 CFH). Too low flow can result in inadequate protection, while too high flow can disrupt the molten pool.
3. Use a high-quality MIG welding wire ( best MIG welding wire for industrial use )
The choice of welding wire type should be matched with the welding material, for example, the ER70S-6 welding wire is ideal for carbon steel welding.
Silk cleaning: ensure that the wire surface is clean and free of oil or rust. Select rust-proof welding wire, and take moisture-proof measures during storage.
4. Adjust the welding Angle and speed
Proper MIG welding angle : keep the Angle between the welding torch and the workpiece at 15 to 20 degrees to ensure the arc stability and uniform distribution of the melting pool.
Optimal MIG welding speed : Maintain a stable welding speed and avoid being too fast or too slow. Welding speed is too fast is easy to lead to welding is not thorough, and too slow may cause overheating phenomenon, or even splash.
5. Maintain the welding equipment regularly( MIG welder maintenance tips )
Check the grounding wire: ensure that the grounding wire contacts well to avoid the arc instability caused by poor contact.
Clean the welding torch: clean the welding torch nozzle and conductive nozzle regularly to prevent blockage or contamination.
Replace worn parts: timely replace the aging conductive nozzle, liner and drive wheel to ensure the normal operation of the equipment.
3. Splash-control cases in industrial applications
Case 1: Automobile manufacturing industry
In the field of automotive manufacturing, MIG welding is widely used in the production of body and parts. Due to the high requirements for welding quality and appearance of automotive components, splash control is particularly important.
A well-known automobile manufacturer has adopted a series of spatter control measures, including optimizing welding parameters, selecting suitable protective gases, using high-quality welding wires, adjusting welding angles and speeds, and maintaining welding equipment regularly. The implementation of these measures successfully reduced the spatter rate by 30%, and improved the welding quality and production efficiency.
Specifically, the manufacturer ensures the stability and controllability of the welding process by precisely setting the welding current, voltage and welding speed. At the same time, they chose a protective gas that matches the base material, effectively reducing oxidation and splashing during the welding process. In addition, they also carry out regular cleaning and maintenance of the welding gun, ensuring the normal operation of the equipment and welding quality.
These splash control cases not only show the practical application effect of MIG welding in the automobile manufacturing industry, but also provide useful reference and reference for other industries.
Case 2: Steel structure processing
In this case, a company specializing in the processing of steel structures found a significant change after the introduction of high-quality welding wires and the implementation of regular equipment maintenance strategies. In particular, the spatter problem generated during welding has been significantly alleviated. This improvement not only significantly reduces the time required to clean up welding spatter, thereby improving work efficiency, but also further reduces additional welding costs due to spatter problems. Through these measures, the company has not only improved production efficiency, but also achieved cost savings, thereby enhancing market competitiveness.
4. sum up
Reducing the MIG welding splash is the key to improving the welding quality and efficiency. Industrial users can significantly reduce splash problems by optimizing welding parameters, selecting suitable protective gases, using high quality wires, adjusting welding angles and speed, and regular maintenance of equipment.
By implementing these measures, you can not only improve welding quality, but also reduce production costs and enhance overall competitiveness. If you are looking for professional MIG welding technical support or equipment recommendations, we offer multiple MIG welder options, including dual pulse and multifunctional equipment to meet your different needs. We also provide detailed information and training on MIG welding technology to help you better understand and apply this technology. Please feel free to contact our professional team or visit our website for more resources.
No matter what kind of welding machine you need, Doughty Welder can provide for your needs. Contact our sales team if you need advice beyond what this article provides. Our team of experts can help you make the right choice.