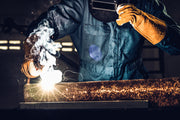
Welding is a key technology in manufacturing, construction and maintenance. Choosing the right type of welding is crucial to ensure welding quality, improve efficiency and reduce cost. This paper will systematically introduce how to choose the correct welding type according to the material, application scenario and process requirements, and provide practical suggestions.
1. Overview of the welding types
1.1 Melting welding
Melting welding is a method of melting and connecting materials by heating. The common types include:
Arc welding: such as manual Stick welding (SMAW) , MIG welding (GMAW) , TIG welding (GTAW).
Gas welding: using oxygen-acetylene flame.
Laser welding: high precision welding, suitable for microelectronics and precision components.
1.2 Pressure welding
Pressure welding is a pressure connection material, and the common types include:
Resistance welding: such as spot welding, seam welding, suitable for automobile manufacturing.
Friction welding: the use of friction heat connection material, suitable for aluminum alloy.
1.3 Bravery welding
Braazing the material by melting filler metal (brder), the base metal does not melt and is suitable for precision connection.
2. Key factors for selecting the welding type
2.1 Material type
Different materials have different requirements for welding types:
Carbon steel: suitable for manual arc welding, MIG welding.
Stainless steel: TIG welding is recommended to avoid oxidation.
Aluminum and aluminum alloy: use TIG welding or MIG welding, and cooperate with argon protection.
Titanium alloy: TIG welding shall be performed under inert gas protection.
2.2 Workpiece thickness
Thin plate (<3mm): suitable for TIG welding or gas welding, to avoid burning through.
Medium plate (3-10mm): MIG welding or manual arc welding.
Thick plate (> 10mm): submerged arc welding or electric slag welding is recommended to improve efficiency.
2.3 Application Scenario
Manufacturing industry: such as car body welding, suitable for resistance welding or robot MIG welding.
Construction industry: steel structure welding, commonly used manual arc welding or submerged arc welding.
Maintenance field: gas welding or manual arc welding, strong flexibility.
2.4 Process requirements
High accuracy requirements: choose laser welding or TIG welding.
High efficiency requirements: MIG welding or submerged arc welding is more suitable.
Cost control: manual arc welding equipment has a low cost, suitable for small-scale operations.
3. Comparison of the advantages and disadvantages of the common welding types
3.1 Manual electric Stick welding (SMAW)
Advantages: simple structure, economic benefits, extensive adaptability.
Disadvantages: low efficiency, the operator needs to have a high technical level.
Applicable occasions: outdoor operation activities, maintenance work, small production.
3.2 MIG welding (GMAW)
Advantages: it has high efficiency, easy to achieve automatic operation, and is suitable for a variety of materials.
Disadvantages: the purchase cost of the equipment is relatively high, and the gas needs to be protected during the use process.
Applicable scenario: suitable for automobile manufacturing, steel structure welding and other fields.
3.3 TIG welding (GTAW)
Advantages: excellent welding quality, especially suitable for sheet and precision welding operations.
Disadvantages: the welding speed is slow, and the technical level of the operator is high.
Applicable scenario: suitable for the welding work of stainless steel, aluminum, titanium alloy and other materials.
3.4. Electrical resistance welding
Advantages: with high efficiency, no additional filling material.
Disadvantages: the equipment purchase cost is higher, and more suitable for a specific shape of the workpiece.
Applicable scenario: suitable for spot welding of automobile body and welding of metal mesh.
4. To select the weld type
4.1 Clear requirements
Before the welding operation, several key parameters need to be defined first, including the type of welding material selected, the specific thickness of the workpiece, the specific requirements for the welding accuracy and the budget range of the whole welding operation.
4.2 Assess the process feasibility
In welding operations, it is necessary to carefully select the most suitable welding type according to the characteristics of the material used and the specific process requirements. This step is crucial because it will directly affect the quality of the welding and the performance of the final product.
4.3 Consider the equipment and cost
In the selection of equipment and process, should pay attention to cost performance, to ensure that while improving efficiency, the cost can be reasonably controlled to achieve the best economic benefits.
4.4 Testing and optimization
During the small-scale trial, we focused on careful adjustment and optimization of process parameters, but not limited to key factors such as current, voltage and welding speed.
5. Case analysis
5.1 Welding selection in automobile manufacturing
Demand: high efficiency, high quality, suitable for mass production.
Selection: resistance welding (spot welding) for body connection, MIG welding for structural parts welding.
5.2 Stainless steel pipe welding
Requirements: high precision, corrosion resistance, no oxidation.
Selection: TIG welding, combined with argon gas protection.
5.3 Aluminum alloy hull welding
Requirements: lightweight, high strength, corrosion resistance.
Selection: MIG welding, protected by aluminum welding wire and argon gas.
6. Future trends and innovation
6.1 Automation and Intelligence
Using robot welding technology and intelligent weld tracking system, production efficiency and product quality will be significantly improved. These advanced technologies not only reduce human error, but also ensure the consistency and accuracy of the welding processes, thus playing an increasingly important role in the industrial manufacturing field.
6.2 Green welding technology
With the enhancement of environmental awareness and the strict implementation of relevant laws and regulations, advanced environmental protection technologies such as low-dust welding rod and energy-saving welder are expected to be more widely used. These technologies can not only help to reduce the harmful smoke and dust produced in the process of welding operation, reduce the environmental pollution, but also improve the energy efficiency, reduce the waste of resources, so as to achieve the purpose of energy saving and emission reduction. In the future of industrial production, the application of these environmental protection technologies will become an important factor to promote the sustainable development of the industry.
6.3 Welding of new materials
With the continuous progress of science and technology and the increasing industrial demand, new welding technologies for composites and high strength alloys will continue to emerge, which will aim to improve the welding efficiency, enhance the strength and durability of the welding site, while reducing the impact on the environment.
7. Summary
Choosing the correct welding type requires a comprehensive consideration of material characteristics, workpiece thickness, application scenarios, and process requirements. The ding quality and efficiency can be significantly improved by clarifying the requirements, evaluating process feasibility and optimizing parameters. In the future, with technological progress, welding will develop in the direction of automation, intelligence and environmental protection, bringing more possibilities for manufacturing and construction.
No matter what kind of welding machine you need, Doughty Welder can provide for your needs. Contact our sales team if you need advice beyond what this article provides. Our team of experts can help you make the right choice.