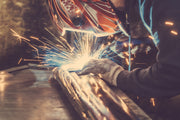
The MTC-215 is the ultimate tool for every level of welder, featuring versatility, power and compact design. This 5-in-1 machine is capable of taking on a wide range of home DIY , maintenance, and industrial-level projects.
5-in-1 multifunction :
MIG welding (GMAW---Gas metal arc welding)
Gasless MIG welding (FCAW---Flux-cored arc welding)
HF DC TIG welding (GTAW---Gas tungsten arc welding)
Stick welding (SMAW---Shielded metal arc welding)
Plasma cutting
This guide will teach you how to set up each welding process, from the necessary physical connection to the setup on the digital display. We will also share some useful welding/cutting tips for a successful welding experience. Before you start working on an exciting project, first read the safety and general overview of welders.
Welding And Plasma Cutting - Safety precautions
First of all, welder is a special job, welding equipment is special equipment. Operators should have sufficient welding, cutting, circuit expertise, and obtain a welder qualification certificate. Operate the machine only after reading and fully understanding the manual and all safety precautions and warnings in the welding operation. Basic safety precautions should always be followed when using tools to reduce the risk of personal injury and equipment damage.
When performing any welding or cutting process including MIC-215:
When welding and cutting equipment is working, it will generate noise, strong light and high temperature sparks, which will cause harm to human hearing, eyes and skin. Correct protective measures and proper operation training are necessary to prevent injury accidents.
-A protective helmet must be worn during welding and cutting operations or observation to protect the eyes, face, neck and ears from arc sparks and bright light.
- Wear flame-retardant gloves, flame-retardant welding/cutting overalls, flame-retardant shoes, welding/cutting helmets or protective hats to prevent burns from arcing, high-temperature sparks or hot metal particles.
- High welding slag temperature, long distance sputtering. When removing welding slag, operators and observers should wear additional safety goggles over safety glasses. Do not touch the welding parts with bare hands to avoid accidental scalding and burns.
Welding and cutting produces a lot of fumes and gas, which is harmful to human health.
- Maintain good ventilation in welding/cutting working environment. Do not weld or cut in confined Spaces. Exhaust and dust removal systems are required.
- Do not weld near degreasing or spraying operations. The heat and electric arcs generated during the operation can react with chlorinated hydrocarbons to form highly toxic and irritating gases that are harmful to humans and can lead to birth defects and, in some cases, cancer.
- If temporary eye, nose or throat discomfort occurs during welding/cutting, it may be due to insufficient ventilation. Stop the operation immediately and take measures to improve ventilation in the work area.
The use and storage of gas cylinders is also an important part.
-The cylinders should be free from high heat and ignition sources.
-Keep the cylinder upright at all times and may be attached or attached to suitable carts, bases, walls, posts or shelves. Ensure that the cylinder valve is closed when not in use.
-If no hose is connected to the cylinder, a dust cover should be installed on the valve port. The pressure reducing valve shall be installed on the cylinder according to the cylinder manufacturer's operating instructions.
During welding and cutting, high temperature flame and arc will be generated, which will cause fire; high temperature welding slag and sparks will also cause fire and explosion.
-Flammable and explosive materials shall not be placed in the welding/cutting area.
-Fire extinguishing equipment such as fire hoses, buckets, sand buckets and portable fire extinguishers must be set up in welding and cutting areas.
-After the welding/cutting operation is completed, check for high temperature sparks or metal that may cause a fire and deal with it promptly.
When performing plasma cutting operations, take extra care to avoid contact with water or moisture. When operating plasma cutting equipment, the open circuit voltage is higher than when welding, so the risk of electric shock is greater. During welding or cutting, wear dry protective clothing to ensure the safety of the insulating metal.
Continue to explore and study welding safety issues. Welding is not only a fascinating hobby, an industry, but also a life passion for many people. However, if precautions against hazards are not taken, welding can quickly become a risk.
DoughtyWelder MCT-215 5-in-1---Overview
The DoughtyWelder MCT-215 welder is built on IGBT inverter technology, giving it a light body and a variety of high-end performance. Before going into the setup steps, let's take a look at its features and use cases.
-Intuitive and easy-to-use LED control panel : The current and voltage display of the LED display, viewing the actual and adjusted values through the knob to improve accuracy and repeatability during your welding process.
-Synergic MIG control:In the synergic operation of MIG/MAG, the wire speed matched with the welding voltage automatically. It supports welding Carbon Steel, Stainless steel, Aluminium sheet, and even Copper sheet.
-Voltage trim:Equipped with trimmer potentiometer on the control panel ,it is more convenient for the voltage compensation of welding to make the welding effect more perfect.
-Equipped with a flux core wire welding feature: this welder eliminates the need for external shielding gas, making it incredibly convenient and cost-effective. The flux core wire creates its own shielding gas when heated, providing excellent weld penetration and reducing the risk of weld defects.
-HT TIG:High frequency booster arc starting, excellent arc starting effect, stable arc, high welding quality.
-Max 16mm Cutting thickness.
-All metals can be welded and cutting: stainless steel, carbon steel, low carbon steel, steel, iron, cast iron, aluminium, Cast iron, Nickel alloy.
Any welding method must have an accurate polarity connection, and welding after the machine is started can form a closed circuit to start the arc. So when choosing any one of the 5 different functions, you have to connect the ground clamp to the welding metal and use the MIG welding torch /TIG welding torch/manual welding torch/plasma welding torch to close the circuit. In the MIG and TIG welding process, it is also necessary to shield the gas, and when the plasma cutting process, it is also necessary to use an external air compressor to pressurize the air. Let's start from the point of view of interpretation.
Want to know how to power up an MTC-215? Come, come, I'll teach you!
There is a power cord with 220V input plug on the back of the machine. However, if you wish to use a welder with a 110V power supply, you will have to connect the conversion wire with a 110V socket to the 220V plug provided by the welder so that the 110V power supply can be connected.
Before you power on, you must have everything necessary for the welding process ready. After plugging the welder into a 110V or 220V socket, just switch the switch button at the back of the machine to the on state, the welder power will turn on, the machine panel will be displayed, and the menu will appear on it. Next, let's explain the Mig setup first.
MIG welding Setup Instructions
To achieve successful MIG welding( GMAW ), you need to set the shielding gas, welding wire, inductance and welding mode on the digital display. Before we discuss these, let's look at some of the specification parameters of the MIG functionality of MTC-215.
Basic parameters of MIG welding:
Rated output current: 30-200A (MIG , 220V) / 30-140A(MIG , 110V).
Open circuit voltage DC: 59V.
Rated welder duty cycle: 60%@200A / 100%@155A.
Voltage range: 15-24V.
Suggested welding wier diameter: 0.6mm-1.0mm.
Shielding Gas For MIG Welding
For MIG welding, you need to use a mixture of 100% CO2 ,100% argon , or the most popular 80% argon (Ar) and 20% CO2 for each sheet, but you can also use different ratios and add helium or oxygen according to your needs.
Using 100% CO2 is the cheapest, but the arc is relatively unstable, the splash rate is large, and the weld surface is poorly formed. It is mainly used for black metals such as low carbon steel and low alloy steel, and can also be used for surfacing of wear-resistant parts, repair welding of cast steel parts and electric riveting welding.
A gas mixture of 80% argon (Ar) and 20% CO2 provides a stable arc with small splash, but it is more expensive and can provide better welding. The welding process produces a hotter, more fluid welding pool with easy axial jet transition. The welded penetration surface is wider than 100% CO2 , but less deep, making it a better choice for thin metals. It is mainly used for the welding of black metals such as carbon steel, alloy steel and stainless steel, especially in the welding of stainless steel.
The 100% argon (Ar) is required for aluminum plate welding. The most common method for welding aluminum and its alloy MIG is jet transition. So the welding current is always greater than the critical current to carry out a stable welding. In the jet transition welding, the constant voltage power supply is combined with the constant speed transmission wire, and the arc regulation effect of the welding power supply is used to maintain a stable jet transition.
Installation of MIG gun and ground clamp
To successfully perform MIG welding, you must use DCEP polarity, which means that your torch is attached to the positive electrode and your ground clamp is attached to the negative electrode. But when welding flux cores and aluminum wires, you must use negative polarity. At this point your ground clamp must be connected to the positive electrode. Switch selection via the conversion line on the panel.
The MIG torch simply needs to be connected to the European-style socket on the panel. After connection, push the MIG gun connection into the unit and tighten the threaded collar to achieve an airtight connection. Since the MIG gun is DCEP when welding MIG, the ground clamp needs to be negative. Therefore, the grounding clamp plug is connected to the center port marked with a "-" sign, and the conversion wire plug on the panel is connected to the center port marked with a "+" sign. The plug works by pushing and twisting the lock after it is aligned to the socket on the brass plug.
How to select tensioner roller and drive roll
The V-groove is used for solid MIG wire feeding, while the W-Groove is used for flux-cored wire. You will recognize the V-Groove roller by the smooth grooves, while the W-Groove has knurled grooves in it.
Wire feeder Composition of:
Installation and adjustment of wire spool
Attention: Before putting the wire spool into the hub shaft, find the locating pin on the shaft and the locating hole on the spool; Then align the hole with the pin and push the wire spool into the hub shaft.The MIG wire spool should be installed to unwind counterclockwise, and feed the wire from under the spool.
Next, cut the bent part of the wire end to ensure that there is a clean, straight wire end. Push the wire through the first lead liner and eventually get it into the MIG welding gun bushing. Finally, lower the inert arm, lift the tensioner, and turn the tensioner to increase the pressure.
Wire feeding pressure regulating
The wire feeding pressure scale is on the pressure regulating handle③. For welding wires of different materials and diameters, the reference value of pressure is as follows:
The pressure scale adjustment values in the above table are for reference only. The actual pressure must be adjusted according to the length of the torch cable, the type of welding torch, the wire feeding conditions and the type of welding wire.
Adjust the drive roll and press the wire with the tensioner roller, so that the wire will not slip when it comes out of the contact tip.
!Attention:
Excessive pressure can make the wire crushed and the coating destroyed;
Excessive pressure will increase the wire feeding resistance, resulting in faster drive roll wear.
After the torch, wire and wire feed wheel have been properly followed, you now need to remove the nozzle of the MIG torch first. Then open the switch on the back panel of the machine, select the MIG mode on the panel, turn the knob on the right side of the front panel to the maximum, and press and hold the gun switch. The wire is then connected to the tip of the MIG torch through the lead wire, and the nozzle is finally attached. The next step is to set parameters.
MIG Welding Parameter setting
When the panel selects MIG welding mode, you will see your current and voltage Settings, welding mode, wire diameter, additional Settings, and more.
The right knob adjusts the current value, the left knob adjusts the voltage value, and the desired Settings can be manually adjusted. When the welding mode is selected SYN MIG, just adjust the current value of the right knob, the voltage parameter will automatically match without adjustment, at this time the left knob plays the role of fine tuning the voltage value.
The four buttons in the bottom row can select the protection gas, welding material type (stainless steel, mild steel, aluminum), wire diameter, inductance adjustment, 2T/4T/SPOT mode, pre flow time, post flow time, and remember your current Settings. After setting the parameters according to the welding requirements, welding can be performed.
Settings when selecting Flux-Cored welding
When the "FLUX" welding mode is selected, the welding process is similar to the MIG welding process, except that it does not require external protection gas, but protects the weld through the gas generated after the burning of the welding wire.
Unlike the MIG welding process, FCAW requires the polarity of the DCEN. This means that the front panel adapter needs to be connected to the port marked "-" and the ground clamp needs to be connected to the positive port marked "+". At this time, it is also necessary to replace the wire feed wheel heel on the wire feeder with a W-shaped slot wire feed wheel.
The required MIG gun is the same as the GMAW, so the installation process is the same as the MIG process described above, and the parameter setting MIG welding process is the same, so the welding can be performed after the parameters are set according to the welding requirements.
How to set up TIG welding on MTC-215
In order to successfully perform TIG welding( GTAW ), you need to plug in the correct protective gas, set the TIG torch and parameters. Before discussing these, let's take a look at some specifications of MTC-215's TIG capabilities:
Basic parameters of TIG welding
Starting mode:HF arcing
Rated output current : 15-200A (TIG , 220V) / 15-120A(TIG , 110V)
Open circuit voltage DC: 59V
Rated welder duty cycle: 60%@200A / 100%@155A
Voltage range: 10.6V-18V
Shielding Gas For TIG Welding
TIG welding, whether welding carbon steel or stainless steel, uses 100% argon shielding gas. Although you can also use argon/helium mixtures to increase the penetration and speed of welding, helium is very expensive, so no special requirements are necessary.
Understanding tungsten electrode
In argon arc welding, tungsten electrode acts as an electrode to conduct current, ignite arc and maintain normal arc combustion. There are many kinds of tungsten electrode, which is easy to be confused as a beginner of TIG welding.
Tungsten electrodes are classified by the main oxide and its percentage of the total electrode mass. Commonly used tungsten electrodes are: pure tungsten (green head), thorium tungsten (red head), lanthanum tungsten (blue head), cerium tungsten (gray head), zirconia tungsten (white head) and rare earth mixed tungsten. For mild steel and stainless steel welded with MTC-215, thorium tungsten and cerium tungsten are recommended. Steel welding operation is good, suitable for DC TIG welding process.
Thorium tungsten is slightly radioactive, so be careful when grinding its tip and follow the manufacturer's safety instructions. Tungsten carbide is not radioactive, but it is not good for welding in the case of high current, but it is also the best choice for welding sheet.
Installation of TIG welding torch and ground clamp
To successfully perform TIG welding, you must use DCEN polarity, which means that your torch is attached to the negative electrode and your ground clamp is attached to the positive electrode.
Connect the TIG welding torch gas-electric integrated cable connector to the gas-electric integrated socket on the front panel and tighten the nut clockwise. Connect the 2-core aviation socket on the torch to the appropriate interface on the welder panel and tighten the screws. Since the TIG gun is DCEN when welding TIG, the ground clamp needs to be positive. Therefore, the grounding clamp plug is connected to the center port marked with a "plus" sign, and the plug works by pushing and twisting the lock after it is aligned with the socket on the brass plug.

TIG Welding Parameter setting
When selecting the TIG welding mode on the panel of the MTC-215, you will see a prefabricated display of current and voltage. Turn the right knob to adjust the current value. The current is fine-tuned according to requirements such as welding metal thickness and welding joint configuration to achieve perfect welding results.
How To Set Up The MTC-215 For Plasma Cutting
In order to successfully perform plasma cutting, you need to properly install the air filter, air access, CUT torch, and parameter Settings. Before discussing these, let's take a look at the specifications of the MTC-215 plasma cutting function:
Basic parameters of Plasma cutting
Rated output current : 20-40A ( 220V ) / 20-30A(110V )
Open circuit voltage DC: 285V
Rated welder duty cycle: 60%@40A / 100%@31A
Voltage range: 88V-96V
Max. cutting thickness: 16mm at 40A , 10mm at 30A.
Compressed air setup and connection supply
Plasma cutting requires the use of an external air compressor to raise the compressed air to be used. Plasma cutting can only use clean, dry compressed air. Do not use oxygen, acetylene, carbon dioxide, combustible gas, or any other bottled gas as this can cause an explosion and serious injury or death. Plasma cutters output high heat and can only be used with compressed air.
Air Filter (Oil-Water Separator)
An air filter has been installed on the MTC-215 rear panel. The purpose is to separate the water from the air and supply the purified air to the plasma cutting torch for use, so that the plasma arc is better and the life of the welding torch is improved. Because if moisture from the air enters the torch, hydrogen and oxygen will erode the consumables more quickly, so the water must be separated out.
Tracheal connection and air pressure regulation
First connect the air compressor to the power supply, use the air pipe to guide the air flow from the air compressor outlet to the air intake valve of the air filter on the back of the welding machine, and clamp the hose with a wrench or sleeve, but not too tight to avoid damage to the hose.
Take a small section of the AIR pipe to connect the air outlet valve of the air filter to the air nozzle marked "air" on the back of the welding machine, and clamp it with a hose clamp. Before tightening the connection, ensure that the hose is not knotted.
Once the trachea is connected, it's ready to be energized. Next, gently pull up the air pressure adjustment knob at the top of the air filter until it clicks and rises, turn it clockwise to set the desired air pressure, and push it down to lock into place.
Installation of cutting torch and ground clamp
Connecting the plasma torch to the ground clamp is easy because they have a dedicated jack at the front of the device. There is no need to worry about polarity, as they cannot be reversed.
Connect the cutting torch gas-electric integrated cable connector to the gas-electric integrated socket on the front panel and tighten the nut clockwise. Connect the 2-core aviation socket on the torch to the appropriate connector on the welder panel and tighten the screws. The ground clamp plug is connected to the jack with the cutting mark in the middle. After the plug is aligned with the socket on the brass plug, it works by pushing and twisting the lock.
Plasma cutting Parameter setting and cutting
When selecting the plasma cutting function, the panel display allows you to adjust the cutting current size, pre flow time, post flow time, 2T/4T operation mode.
To change the current output, you can adjust it by turning the right knob. Front and rear airflow timing allows you to customize how much gas is blown out, how much air you want to use to clean the area before cutting, and how much air to use to cool the torch, all of which can be set according to the actual situation.
2T/4T Operation Mode: Used to select the 2T/4T function. When the "2T" function is used, the torch switch must be held down during the cutting process, and the cutting will stop after release. "4T" function, press the torch switch to release the current, you can start cutting work, and then press the torch switch to stop cutting.
After the parameters are set, you can start the plasma arc, you need to press the gun switch on the torch, the compressed air is released, at this time the gun nozzle contact with the metal, and slightly lift the tip, this will start the arc, and then by dragging the torch can be performed metal cutting. Adjust the cutting speed according to the thickness of the metal being cut. Thicker metal requires a slower moving speed, while thinner volume rules can cut faster.
Finally, the manual stick welding setting of MTC-215
For manual stick welding ( SMAW ), compared to other welding methods of MTC-215, it is the simplest and easiest to set up, you only need to connect the correct polarity and output current Settings. But before we get into that, let's take a look at its basic parameters:
Basic parameters of Stick welding:
Starting mode:DC MMA
Rated output current : 25-180A ( 220V ) / 25-120A( 110V )
Voltage range: 21V-27.2V
Open circuit voltage DC: 59V
Rated welder duty cycle: 60%@180A / 100%@139A
Suggested Electrode Max. : 5mm
Electrode type:E7018 , E6013
Connection between the welding clamp and the ground clamp
The bonding process is suitable for DCEP or DCEN polarity, and the positive or negative DC electrode is selected according to the thickness, type and welding requirements of the welding material.
Dc positive electrode (DCEN) : also known as DC reverse connection, that is, the welding gun (or electrode) is connected to the negative electrode of the power supply, and the workpiece is connected to the positive electrode of the power supply. Under this connection, the workpiece temperature is relatively high, the melting depth is larger, the weld is formed well, and the splash is small, which is suitable for welding thin sheet.
Dc inverse electrode (DCEP) : also known as DC positive connection, that is, the welding gun (or electrode) is connected to the positive electrode of the power supply, and the workpiece is connected to the negative electrode of the power supply. Under this connection, the welding gun (or electrode) has a fast melting speed and a large consumption, which is suitable for welding thick plates.
To set up the rod welding process in DCEP mode, you need to fix the welding rod wire to the positive terminal marked "+" on the front panel and the ground clamp to the negative terminal marked "-".
If rod welding is set in DCEN mode, reverse the connection. The welding wire is connected to the negative terminal, while the ground clamp is connected to the positive terminal.
Stick Welding Parameter setting
When welding the SMAW of CTM-215, after determining that you need to weld the plate, connect the ground wire and the welding wire to the corresponding polarity, and after the machine is powered on, you can modify the current output value by turning the knob on the right, just like TIG welding. In this way, you can contact the electrode with the workpiece, and then lift the electrode slightly, the arc is ignited, and the normal welding can be done.
End of the message
The DoughtyWelder MTC-215 is a versatile welding device with an intuitive and easy-to-use digital display panel design that ensures easy operation and easy parameter setting, however, for beginners, it will be helpful to read a detailed operating guide. As you adjust the welder several times by hand, this skill will gradually become familiar, allowing you to perform your welding skills in any situation.In particular, it is reminded that you must wear safety protective equipment before welding and cutting, and strictly comply with local safety codes and regulations. If you are in doubt about certain safety details, it is strongly recommended to carry out the necessary research and learning before performing welding or cutting operations to ensure safety first.