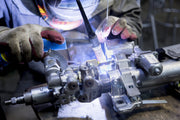
Introduction to Aluminum Welding Techniques
Aluminum welding is a specialized skill requiring precision, the right tools, and an understanding of different welding methods. Two of the most popular techniques for welding aluminum are Metal Inert Gas (MIG) and Tungsten Inert Gas (TIG). Both methods have unique advantages and challenges, making the choice between a Mig vs. TIG aluminum welder critical for achieving optimal results. This guide explores their differences, applications, and how to choose the right method for your project.
Understanding MIG Welding for Aluminum
How MIG Welding Works
MIG welding uses a continuously fed wire electrode and inert shielding gas (typically argon or a mix) to join metals. When welding aluminum, a MIG aluminum welder requires a spool gun or push-pull system to handle the soft aluminum wire, preventing tangling and ensuring smooth feeding.
Advantages of MIG Welding Aluminum
-
Speed: MIG welding is faster than TIG, ideal for high-volume projects.
-
Ease of Use: Less skill-intensive, making it suitable for beginners.
-
Thicker Materials: Excels with aluminum sheets thicker than 1/8 inch.
Limitations of MIG Welding Aluminum
-
Spatter Issues: Aluminum’s high thermal conductivity can lead to excess spatter.
-
Equipment Costs: Requires specialized accessories like spool guns.
-
Aesthetic Finish: Produces rougher beads compared to TIG.
Exploring TIG Welding for Aluminum
How TIG Welding Works
TIG welding uses a non-consumable tungsten electrode and filler rod, with argon gas shielding the weld pool. A TIG aluminum welder requires alternating current (AC) to break aluminum’s oxide layer, ensuring clean, strong welds.
Advantages of TIG Welding Aluminum
-
Precision: Delivers superior control for intricate welds.
-
Aesthetic Quality: Produces smooth, visually appealing beads.
-
Thin Materials: Ideal for aluminum sheets under 1/8 inch.
Limitations of TIG Welding Aluminum
-
Steep Learning Curve: Demands significant skill and practice.
-
Slower Process: Not suitable for high-volume production.
-
Equipment Complexity: Higher upfront costs for advanced machines.
Mig vs. TIG Aluminum Welder: Key Differences
Welding Speed and Efficiency
-
MIG: Faster deposition rates, perfect for large-scale projects.
-
TIG: Slower but offers unmatched precision for detailed work.
Skill Level and Training
-
MIG: Easier to learn, ideal for hobbyists or repair shops.
-
TIG: Requires advanced technique, favored by professional fabricators.
Material Thickness and Application
-
MIG: Best for thicker aluminum (e.g., automotive frames, structural components).
-
TIG: Optimal for thin materials (e.g., aerospace parts, artistic sculptures).
Cost Considerations
-
MIG: Lower labor costs but higher consumable expenses (wire, gas).
-
TIG: Higher labor costs due to slower speeds but minimal material waste.
Common Challenges in Aluminum Welding
Oxide Layer Removal
Aluminum’s oxide layer melts at a higher temperature than the base metal. Both Mig and TIG aluminum welders must address this, but TIG’s AC current handles it more effectively.
Heat Management
Aluminum dissipates heat quickly. MIG’s higher heat input helps, while TIG requires careful amperage control.
Filler Material Selection
Choose filler alloys (e.g., 4043 or 5356) based on the application. TIG allows more flexibility here.
How to Choose Between a MIG and TIG Aluminum Welder
Project Requirements
-
Volume: For mass production, a MIG aluminum welder saves time.
-
Detail: For artistic or precision work, a TIG aluminum welder is superior.
Budget Constraints
-
Initial Investment: MIG systems are generally cheaper but require accessories.
-
Long-Term Costs: TIG may save money on rework for critical applications.
Operator Expertise
-
Beginners may prefer MIG, while seasoned welders can leverage TIG’s capabilities.
After a personal in-depth analysis and discussion of the MIG and TIG methods of welding aluminum and the basic differences between the two techniques, you will be able to more wisely choose the right welding machine for your job to complete your project. Aluminum welding is a challenging job, and two of the easiest and most widely used methods are MIG welding and AC TIG welding. DoughtyWelder offers both. Our DoughtyWelder MIG-205 and TIG-200P AC/DC machines are both up to the task. Next, we will compare the two machines to help you gain a deeper understanding and choose the equipment that suits your needs.
Picture |
![]() |
![]() |
Model |
MIG-205 |
TIG-200P AC/DC |
Welding Process For Aluminum |
MIG | AC TIG |
Polarity |
DCEP | AC |
Protective gas |
100% Argon | 100% Argon |
Commonly used Welding wire |
ER4043 and ER5356 wire spools | ER4043 and ER5356 TIG rod |
Filler Metal Feeding Method |
Using the MIG-200P wire feeder to feed wire through the graphene-lined tube of the welding gun | Manually push the TIG wire evenly into the weld pool |
Welding speed |
Faster | Slower |
Welding quality |
Medium | Excellent |
Welding thin aluminum plates |
Difficult. It is easy to burn through when welding. | Easier. TIG pulse, foot pedal function control and other auxiliary parameter adjustment, you can easily control the heat input |
Welding thick aluminum plates |
Great | Great. But it requires high current welding |
Process Cleanliness |
Dirtier. The welding process produces sparks and smoke | Clean. Smoke-free and spark-free welding process |
Available parameter adjustments to improve welding quality |
Inductance, hot start | AC balance, AC frequency, Starting current, Up-slope, Down-slope, Pre-flow, Post-flow, Crater current, Pulse frequency, and pulse width. |
FAQs About Mig vs. TIG Aluminum Welders
Can You Use a Standard MIG Welder for Aluminum?
Yes, but only with a spool gun or push-pull system to feed the soft aluminum wire.
Why Use AC Current for TIG Welding Aluminum?
AC current cleans the oxide layer during the electrode-positive cycle, ensuring stronger welds.
Which Method Is Better for Automotive Aluminum Repair?
MIG is faster for thick panels, while TIG is preferred for engine components or custom builds.
Conclusion
Choosing between a Mig vs. TIG aluminum welder depends on your project’s scale, budget, and desired finish. MIG offers speed and simplicity, while TIG provides precision and aesthetic quality. By understanding their strengths, you can select the ideal method for your aluminum welding needs.
No matter what kind of welding machine you need, Doughty Welder can provide for your needs. Contact our sales team if you need advice beyond what this article provides. Our team of experts can help you make the right choice.
🧐🧐🧐You might like the following:
2. How to MIG welding aluminum for beginners
3.Based on 4000+ customer reviews, this plate gold welding artifact stan