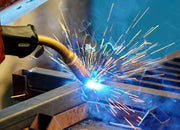
MIG welding (Metal Inert Gas welding) is a versatile and widely used process in fabrication, automotive repair, and industrial manufacturing. One of its key advantages is its adaptability to weld metals of varying thicknesses. However, achieving consistent results requires understanding how to adjust settings, techniques, and materials for each scenario. In this guide, we’ll explore how to MIG weld different metal thicknesses, covering everything from thin sheet metal to thick structural steel.
Understanding Metal Thickness in MIG Welding
1.1 Why Metal Thickness Matters
MIG welding relies on balancing heat input, wire feed speed, and shielding gas to create strong, clean welds. Metal thickness directly impacts these variables:
-
Thin metals (e.g., 24-18 gauge) require low heat to prevent burn-through.
-
Medium metals (e.g., 1/8" to 1/4") need moderate heat for proper penetration.
-
Thick metals (e.g., 1/2" and above) demand high heat and multi-pass techniques.
Using incorrect settings for a given thickness can lead to defects like porosity, warping, or incomplete fusion.
1.2 Tools and Equipment for Different Thicknesses
Before diving into techniques, ensure you have:
-
A MIG welder with adjustable voltage and wire feed speed.
-
Wire diameter: 0.023" for thin metals, 0.030"/0.035" for medium/thick metals.
-
Shielding gas: 75% Argon/25% CO₂ (C25) for steel; 100% Argon for aluminum.
-
Contact tips and nozzles sized to match your wire.
MIG Welding Thin Metals (24 Gauge to 1/8")
2.1 Challenges of Thin Metal MIG Welding
Thin metals (e.g., automotive panels, HVAC ducts) are prone to:
-
Burn-through: Excessive heat melts the base metal.
-
Warping: Uneven heat distribution causes distortion.
-
Poor penetration: Insufficient heat creates weak welds.
2.2 Ideal Settings for Thin Metals
-
Wire Diameter: Use 0.023" wire for precise control.
-
Voltage: Set between 14–18 volts.
-
Wire Feed Speed: 100–200 inches per minute (IPM).
-
Shielding Gas Flow Rate: 15–20 CFH.
2.3 Techniques for Thin Metal
-
Stitch Welding: Tack weld in short bursts (1–2 seconds) to manage heat.
-
Backstepping: Weld backward over previous tacks to cool the metal.
-
Use a Heat Sink: Clamp copper or aluminum bars behind the joint to absorb excess heat.
2.4 MIG Welder for thin metal
Dual-Pulse MIG welding technology proves particularly advantageous when working with thin-gauge metals. While this capability was historically restricted to premium-tier industrial equipment, it is now accessible through the DoughtyWelder MIG-200P dual-pulse MIG welder.
DoughtyWelder MIG-200P Multi-Process MIG Aluminum Welder
This feature modulates the heat generated by the pulsed welding arc, enabling precise thermal control while maintaining exceptional arc stability and minimizing spatter. Aesthetically, it achieves TIG welding quality using MIG welding equipment.
MIG Welding Medium-Thickness Metals (1/8" to 1/4")
3.1 Balancing Penetration and Speed
Medium-thickness metals (e.g., brackets, frames) require a balance between penetration and travel speed. Common issues include:
-
Incomplete Fusion: Moving too fast leaves gaps.
-
Excessive Spatter: High voltage or incorrect gas coverage.
3.2 Recommended Settings
-
Wire Diameter: 0.030" or 0.035".
-
Voltage: 18–22 volts.
-
Wire Feed Speed: 200–300 IPM.
-
Gas Flow Rate: 20–25 CFH.
3.3 Techniques for Medium Metal
-
Drag Technique: Angle the gun 10–15° and drag it toward the weld pool for deeper penetration.
-
Bead Sequencing: For wider joints, weld the root pass first, followed by filler passes.
-
Pulse MIG Welding: Reduces spatter on critical projects.
MIG Welding Thick Metals (1/4" to 1/2"+)
4.1 Overcoming Heat Dissipation Challenges
Thick metals (e.g., structural beams, heavy machinery) demand high heat input but risk:
-
Slag Inclusions: Poor cleaning between passes traps impurities.
-
Cracking: Rapid cooling stresses the weld.
4.2 Optimal Settings for Thick Metal
-
Wire Diameter: 0.035" or 0.045".
-
Voltage: 22–28 volts.
-
Wire Feed Speed: 300–450 IPM.
-
Preheating: Heat the metal to 200–300°F for reduced thermal shock.
4.3 Multi-Pass Welding Strategies
-
V-Groove Preparation: Bevel edges at 30–45° to ensure full penetration.
-
Weave Technique: Oscillate the gun in a zigzag pattern to cover wider joints.
-
Interpass Cleaning: Remove slag with a wire brush between passes.
4.4 MIG Welder for thick-thickness steel
When welding medium-thickness metals ranging from 1/4 inch to 1/2 inch, welding equipment with a rated current output of 200-250 amps operating at 220V input voltage is essential. Such power-rated machines deliver adequate thermal energy to achieve proper fusion on thicker material sections. Our technical recommendation specifies the DoughtyWelder MIG-255D unit for this application.
DoughtyWelder MIG-255D Multi-Process MIG Welding Machine
Engineered for superior performance, this welding system combines an all-in-one trailer-integrated structure with a 15kg integrated wire feed spindle. Operating at a rated current of 250A , it accommodates most DIY applications, delivering single-pass weld penetration up to 1/4" (0.6 cm) on mild steel substrates. The MIG-255D eliminates the need for advanced pulse functionality, positioning it as a cost-efficient choice for entry-level users. Full power utilization requires a dedicated 220V circuit.
Special Considerations for Different Metals
5.1 MIG Welding Stainless Steel
-
Use tri-mix gas (90% Helium/7.5% Argon/2.5% CO₂).
-
Keep heat input low to prevent carbide precipitation.
5.2 MIG Welding Aluminum
-
Push Technique: Angle the gun 10–15° forward to improve gas coverage.
-
Spool Gun: Prevents wire feeding issues with soft aluminum wire.
5.3 Galvanized Steel Welding
-
Grind off zinc coating near the weld area to avoid toxic fumes.
-
Increase ventilation and wear a respirator.
Troubleshooting Common MIG Welding Issues
6.1 Burn-Through on Thin Metal
-
Lower voltage and wire speed.
-
Increase travel speed.
6.2 Lack of Penetration on Thick Metal
-
Increase voltage and preheat the metal.
-
Use a wider joint preparation.
6.3 Excessive Spatter
-
Check gas flow and replace clogged nozzles.
-
Adjust voltage to match wire feed speed.
Safety Tips for MIG Welding All Thicknesses
-
Wear ANSI-approved PPE: helmet, gloves, and flame-resistant clothing.
-
Ensure proper ventilation to avoid inhaling fumes.
-
Inspect equipment for gas leaks or damaged cables.
FAQs About MIG Welding Metal Thickness
Can I use the same wire for all metal thicknesses?
No. Thin metals work best with 0.023" wire, while thicker metals require 0.035" or 0.045".
How do I prevent warping on thin sheets?
Use stitch welding, heat sinks, and clamp the workpiece securely.
What’s the maximum thickness I can MIG weld?
With proper multi-pass techniques, MIG welding can handle metals up to 1/2" thick. Beyond that, consider submerged arc welding (SAW).
By mastering how to MIG weld different metal thicknesses, you’ll expand your capabilities across diverse projects. Always test settings on scrap metal first, and document your parameters for repeatable results. Whether you’re crafting custom automotive parts or repairing heavy equipment, precision in adjusting for thickness ensures durable, high-quality welds.
No matter what kind of welding machine you need, Doughty Welder can provide for your needs. Contact our sales team if you need advice beyond what this article provides. Our team of experts can help you make the right choice.
🧐🧐🧐You might like the following:
1.Seven "minefields" to pay attention to when TIG welding
2. How to MIG welding aluminum for beginners
3.Based on 4000+ customer reviews, this plate gold welding artifact stan