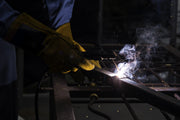
Master the Art of Electric Welding: Understanding Principles and Electrode States.
The principle of electric welding
Electrode arc welding( SMAW ) is a welding technique that uses a electrode as an electrode and filler metal. In the welding process, one end of the electrode is ignited to produce an arc, and the high temperature of the arc makes the electrode and the surface of the workpiece melt. As the molten metal cools, a weld is formed.
In the stick welding, the circuit at the arcing stage shows a short circuit, which causes the voltage to plummet and the current demand to increase. Once the arc is successful, in order to maintain the stability of the arc, the liquid of the electrode and the molten pool still maintains the short-circuit state, the voltage continues to decrease, and the current is still maintained at a high level. When the transition phase ends, the welding enters a stable state, the voltage gradually rises, and the current is correspondingly reduced.
The thrust circuit is designed to automatically increase the output current when the output voltage drops below 15V, especially in the case of short circuit, forming an external drag characteristic to effectively prevent the electrode from sticking. The arc starting circuit briefly raises the preset voltage at each start to increase the arc current, thus simplifying the arc starting process.
The arcing current refers to the maximum current output that the welding machine can provide in the arcing stage.
Thrust current refers to an additional current provided by the welding machine during the welding process in order to ensure a stable transition of hot metal and prevent the welding rod from sticking.
The welding current is the continuous working current provided by the welding machine in the normal welding operation.
State of the electrode during operation
In the welding process, the electrode acts as an electrode, which is not only responsible for conducting current and igniting the arc, ensuring that a continuous and stable arc is formed between the electrode and the base metal, thus providing the heat required for fusion welding. At the same time, the electrode is also added to the weld as a filler material, becoming a key component of the weld metal. Therefore, the composition and quality of the electrode will directly affect the chemical composition, mechanical properties and physical properties of the weld metal.
In addition, the electrode also has a significant impact on the stability of the welding process, the appearance quality of the weld and the welding production efficiency. The welding core is the metal core part of the welding rod, in order to ensure the quality of the weld, the content of various metal components in the welding core has a clear specification. In particular, harmful impurities (such as sulfur, phosphorus, etc.) are strictly controlled, and the quality of the core metal must be higher than that of the base metal.
Bare electrode without coating can not be arc welding, because this will lead to poor arc stability, serious spatter, poor weld forming. After a long time of practice, it is gradually found that the performance of the electrode is significantly improved after the welding core surface is coated with a specific mineral material (that is, the electrode coating).
What are the skills of vertical and overhead welding?
In arc welding technology, there are four basic welding positions: flat welding, horizontal welding, vertical welding and overhead welding. In these welding positions, horizontal and horizontal welding are less difficult to operate than vertical and overhead welding. On the other hand, vertical welding and overhead welding are more challenging because of their higher technical requirements. For vertical welding and overhead welding skills, in addition to daily diligent study and practice, the following points need to be paid special attention:
First of all, as we all know, in the welding process, the molten metal will be affected by gravity, if the operation is improper, the metal is easy to flow downward, resulting in increased difficulty in welding molding, easy to produce welding tumors, affecting the beauty of the weld. In addition, improper welding may also form grooves on both sides of the weld, resulting in non-fusion and slag inclusion defects.
Secondly, when performing vertical and overhead welding, it is very important to select the appropriate welding parameters. The operation method of small current, continuous welding and short arc is recommended. At the same time, in the welding process, special attention should be paid to the control of welding Angle. In vertical welding, the Angle between the electrode and the weld should be maintained between 80 and 90 degrees; When welding, the Angle between the electrode and the welding direction should also be maintained at 80 to 90 degrees.
Thirdly, in the operation process of vertical welding and overhead welding, in addition to selecting the appropriate welding parameters, the choice of rod transport mode can not be ignored. For vertical welding, it is recommended to use crescent shape or sawtooth shape. When welding upward, it is advisable to use the short arc straight shape or oblique circle.
To sum up, vertical welding and overhead welding have certain technical difficulties for welding workers, especially beginners, so they need to improve their welding skills through a lot of practice and experience accumulation.
Fortunately, the Doughtywelder ARC-200D welding machine has the ability to burn almost any type of electrode at a variety of angles, making it easy for users to cope with a variety of welding operations.
Doughtywelder------ARC-200D
What should I do when my hand shakes during welding?
First, maintaining a stable state of mind and correct posture is key. When welding, the arm should be relaxed as much as possible to avoid excessive tension resulting in hand shaking. Secondly, you can try to use welding fixtures or fixtures to stabilize the workpiece and reduce the burden on the hand. In addition, practicing breath control and maintaining an even breathing rhythm can also help reduce involuntary hand shaking. Finally, through repeated practice, familiar with the welding process and skills, you can gradually improve the stability and control ability of the hand.
During the welding process, some auxiliary measures can also be taken to further improve stability. For example, use shock pads or supports to reduce shaking caused by ground shaking or instability. At the same time, choose the right welding equipment and tools to ensure that their weight and balance are suitable for long-term operation to reduce arm fatigue. In addition, regular rest and hand muscle stretching exercises can effectively prevent and reduce hand shaking.
Through the application of these comprehensive methods, welding workers can gradually overcome the problem of hand shaking and improve the quality of welding.
Dissimilar steel welding and electrode selection skills
The main problems of dissimilar steel welding:
- Non-uniformity of chemical composition of welded joints and the resulting heterogeneity of organizational structure and mechanical properties
- Stability of interface organization
- Stress and deformation complexity characteristics
The basic principles of the selection of dissimilar steel welding materials:
- The selected welding material must ensure the key properties required for the design of dissimilar steel welded joints, including but not limited to mechanical properties, heat resistance and corrosion resistance;
- The selected welding materials should meet the dilution rate, melting point and other physical properties of the welding parts to ensure the smooth progress of the welding process;
- Under the premise of ensuring that the welded joint has no cracks and other defects, if the strength and plasticity of the weld metal cannot be taken into account at the same time, priority should be given to the selection of filling materials with good plasticity;
- Welding materials should be economical, easy to obtain, and show excellent welding process performance.
Carbon steel and low alloy structural steel or dissimilar low alloy structural steel welding electrode selection:
--The selected electrode must ensure that the strength of the weld metal and its joint exceeds the strength of the steel on the lower side of the strength, and the plasticity and impact toughness of the weld must not be lower than the level of the steel on the higher side of the strength but the plasticity and toughness are poor. In other words, the strength, plasticity and toughness of the weld should meet or exceed the minimum standards of the material to be welded.
--It is usually recommended to use a low hydrogen electrode to ensure that the weld metal has good crack resistance and plasticity.
--It is recommended that the carbon content in the welding wire is low, while the manganese content is high, and the ratio of manganese to silicon is increased to reduce the probability of hot cracking.
According to the JB/T4709-2000 standard, the weld metal between carbon steel and low alloy steel of different strength levels should meet the mechanical properties requirements, and its tensile strength should not exceed the maximum value specified in the higher strength base metal standard.
Welding electrode selection of carbon steel, low alloy structural steel and pearlite heat resistant steel:
--Under normal circumstances, the use temperature of dissimilar joints is not too high. Therefore, the welding material that matches the base material with a lower alloy content should be selected to ensure the mechanical properties of the welded joint at room temperature. The strength of the joint shall not be lower than the lower of the standard values specified by the two base materials.
--You can consider using carbon steel welding rods or heat-resistant steel welding materials. However, the welding process must follow the standard of pearlitic heat-resistant steel. For example, when welding A3 or 16Mn with 15CrMo, J507 or R207 electrodes are recommended.
--For the case of large structural rigidity and no heat treatment after welding, A307 electrode can be used. However, it should be noted that the maximum operating temperature of such dissimilar steel joints should not exceed 350 ° C.
Dissimilar pearlite heat-resistant steel welding electrode selection:
--Under the same operating temperature conditions, it should be ensured that the steel requirements of lower strength are met, and the content of alloying elements in the weld should not be lower than that of the base metal with fewer alloying elements. At the same time, the thermal strength of the weld should equal or exceed the base metal. In general, the use of low hydrogen electrode is recommended.
--In specific cases, in order to prevent carbon migration during the welding process, during post-welding heat treatment or during use, and to ensure the high temperature performance of the joint, a electrode with an alloying element content between two base materials should be selected.
For example, in the case of 12Cr1MoV and 10CrMo910 pipeline welding, when R307, R407, R317, J507 welding rods are selected, the room temperature mechanical properties of the welded joint can reach (welding process evaluation results). However, according to the requirements of high temperature lasting strength, R407 and R317 welding rods can meet the use standards; The R307 and J507 do not meet these requirements.
--If the product standard does not allow or the site conditions do not allow pre-welding and post-welding heat treatment, you can consider using austenitic welding materials. However, for pearlite dissimilar joints at high temperatures, austenitic welding materials should be used with caution.
--For dissimilar steel joints that may form a diffusion layer at the use temperature, it is recommended to weld an isolation layer on the groove surface, and the isolation layer metal should contain Cr, V, Ti and other elements that can form strong carbides.
Welding electrode selection between austenitic stainless steel:
When welding dissimilar austenitic steels, the key is to prevent defects such as thermal cracking, intergranular corrosion and σ embrittlement in welded joints.
--The electrode should be selected according to the base material with a lower alloy content or the alloy content between the two.
--The welding rod containing austenite-ferrite biphase structure is used to ensure that the weld metal contains 3-5% ferrite, thus enhancing the crack resistance and corrosion resistance of the joint.
--Strictly control the carbon content of weld metal.
For example, when welding 1Cr18Ni9Ti and 0Cr18Ni12Mo2Ti, A132, A137, A202, A207, A212 and other types of electrode can be selected.
Final idea
Mastering the variety of skills in welding technology is significant for improving the skill level of daily welding operations, and thus adding added value to professional work. If the technique is used properly, it can effectively overcome the many challenges faced by bonding, application-specific and inverter welding processes. Therefore, an in-depth understanding of the principles behind various welding techniques is particularly critical. The purpose of this paper is to explore and explain these principles in order to improve the understanding and application of welding technology.
No matter what kind of welding machine and plasma cutting machine you need, we can meet your needs. If you need advice beyond what is provided in this article, please contact our sales team. Our team of experts can help you make the right choice...
🧐🧐🧐You might like the following:
1. Ok, then let's talk about the most basic: Stick Welder
2. Mastering MIG, TIG, and Stick Welding in 3 Easy Steps
3. MTC-215 5-in-1 Multi-Functional Welder & Cutter User Guide