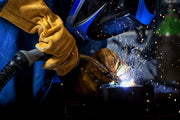
Technical background of double pulse MIG welder
As an outstanding representative of modern welding technology, double pulse MIG welding machine has a deep technical background and is full of innovation. Based on the traditional MIG welder, the technology introduces the double pulse current waveform to realize the fine control of the welding process. The double pulse current waveform is formed by superposition of high frequency pulse and low frequency pulse. The high frequency pulse is responsible for maintaining the stability of arc and the transition of droplet, while the low frequency pulse is to stir the weld pool to promote the uniform distribution of weld metal and fine grain. This unique current waveform design makes the dual pulse MIG welder exhibit excellent performance in aluminum alloy MIG welding.
According to the experimental data, the welding depth and width of the weld are significantly improved when the double pulse MIG welding machine is used for aluminum alloy mig welding, and the strength and toughness of the weld metal are better than the traditional MIG welding machine. For example, when welding 6061 aluminum alloy sheet with a thickness of 10mm, the double pulse MIG welding machine can reach a depth of 5.5mm, while the traditional MIG welding machine is only 4.8mm. In addition, the double pulse MIG welding machine can also effectively reduce welding defects, such as pores, cracks, etc., and improve welding quality. This advantage is due to the stirring effect of double pulse current on the molten pool, which can break the gas and impurities in the molten pool, promote its floating and discharge the molten pool.
In practical applications, double pulse MIG welding machine has been widely used in aerospace, automobile manufacturing, ship construction and other fields. In the aerospace field, for example, the requirements for welding quality are extremely high, and any small welding defect can lead to serious consequences. Therefore, with its excellent welding performance and stability, the double pulse MIG welding machine has become the preferred equipment for aluminum alloy welding in the aerospace field. For example, in the fuselage manufacturing process of a certain type of aircraft, the use of double-pulse MIG welding machine to weld aluminum alloy skin not only improves the welding efficiency, but also ensures that the quality of the weld meets the design requirements.
In summary, the double pulse MIG welding machine has a deep technical background and is full of innovation, and its application prospects in aluminum alloy MIG welding are broad. With the continuous progress of technology and the in-depth promotion of application, double pulse MIG welder will certainly play an important role in more fields and contribute more to the development and progress of welding technology.
Principle of double pulse MIG welding machine
The core of the double pulse MIG welding machine is its unique double pulse current waveform characteristics, which significantly improves the accuracy and efficiency of aluminum alloy MIG welding. The double pulse waveform consists of a series of alternating high and low current pulses, each high pulse followed by a low pulse, forming a "pulse-intermittent-pulse" cycle pattern. This waveform design not only optimizes the heat input distribution in the welding process, but also enhances the stirring effect of the weld pool and effectively reduces the welding defects.
Specifically, the high pulse stage provides enough energy to melt the base metal and the welding wire to form a stable molten pool; The subsequent low pulse stage promotes the cooling and solidification of the molten pool by reducing the heat input, while using the natural convection and electromagnetic force in the molten pool to achieve uniform mixing. This stirring action helps to refine the weld structure and reduce the occurrence of defects such as pores and cracks. According to the experimental data, the porosity of the weld can be reduced to less than 50% of the traditional MIG welding machine when the double pulse MIG welding machine is used for aluminum alloy welding.
In the welding process of double pulse MIG welder, the setting of pulse parameters plays a crucial role in the welding quality. Pulse frequency, pulse width, pulse current peak value and other parameters directly affect the dynamic behavior of weld pool, heat input distribution and weld formation. For example, when the pulse frequency is increased from 50Hz to 200Hz, the stirring effect of the weld pool is significantly enhanced, effectively promoting the discharge of gas in the weld pool and reducing the generation of welding pores. According to the experimental data, the porosity of welding under high frequency pulse can be reduced to less than 30% of traditional MIG welding, which significantly improves the welding quality.
The adjustment of pulse width is directly related to the uniformity of welding heat input. A wider pulse width can increase the heat input and promote the penetration depth of the weld metal, but it may also lead to the expansion of the overheated zone and affect the mechanical properties of the welded joint. In contrast, a narrow pulse width can reduce the heat affected zone, but it may cause defects such as non-fusion or non-penetration due to insufficient heat input. Therefore, in practical applications, it is necessary to accurately control the pulse width according to the thermal conductivity, melting point and other characteristics of aluminum alloy materials to achieve accurate control of welding heat input.
The setting of pulse current peak value is directly related to the stability of welding arc and the form of droplet transition. Higher peak pulse current can produce stronger arc force, promote the spray transition of the droplet, and improve the welding speed and production efficiency. However, too high a peak current may also lead to an increase in welding spatter, affecting the appearance quality of the weld. Therefore, in aluminum alloy MIG welding, it is necessary to combine specific welding tasks and optimize the peak pulse current to achieve a good balance between welding speed and welding quality.
In addition, the dual pulse MIG welding machine also has an intelligent control system, which can monitor the voltage, current and other parameters during the welding process in real time, and automatically adjust the pulse parameters according to the preset welding procedure to meet the needs of different welding conditions. This intelligent control method not only improves the stability and reliability of the welding process, but also reduces the requirements for the skill level of the operator, and provides a strong support for the wide application of aluminum alloy MIG welding.
Analysis of material characteristics and weldability of aluminum alloy
Aluminum alloy, as an indispensable lightweight high-strength material in modern industry, its unique physical and chemical properties put forward special requirements for the MIG welding process. First of all, aluminum alloy has a high thermal conductivity and electrical conductivity, which means that during the welding process, heat transfer is rapid, and the weld area is easy to cool, which may lead to defects such as cracks and pores in the welded joint. Therefore, when setting the MIG welding process parameters, it is necessary to fully consider the thermal sensitivity of the aluminum alloy, and ensure the weld quality by accurately controlling the welding current, voltage and welding speed. For example, when the welding current is controlled in the range of 150-250A and the welding speed is maintained at 50-100mm/s, the mechanical properties of aluminum alloy MIG welded joints can be optimized.
In addition, aluminum alloys are easy to react with oxygen in the air to form a dense alumina film. This layer of film will hinder the wetting and bonding of the weld pool and the welding wire during the welding process, resulting in poor welding. Therefore, before aluminum alloy MIG welding, strict surface cleaning must be carried out, such as the use of mechanical grinding, chemical cleaning and other methods to remove oxide film and oil. According to actual cases, after strict surface treatment of aluminum alloy sheet, the tensile strength of its MIG welded joint can be increased by about 15%, while significantly reducing the incidence of porosity and other defects.
In terms of weldability analysis, the weldability of aluminum alloy is affected by multiple factors such as alloy composition, heat treatment state and welding process parameters. For example, aluminum alloys with high magnesium content (such as 5 series aluminum alloys) are prone to hot cracks during welding, which need to be improved by adjusting welding process parameters, preheating or post-welding heat treatment. The 6 series aluminum alloy is widely used in aerospace, automobile manufacturing and other fields because of its good weldability and mechanical properties. According to the evaluation standard of International Institute of Welding (IIW), the weldability of aluminum alloy can be divided into three grades: easy weldability, difficult weldability and difficult weldability, which provides an important basis for the selection and optimization of welding process.
Aluminum MIG welding process parameter setting
In aluminum alloy MIG welding, the precise setting of process parameters is the key to ensure welding quality and efficiency. MIG welding process parameters mainly include welding current, welding voltage, welding speed, wire feed speed and protection gas flow. The reasonable selection and adjustment of these parameters directly determine the formation of the weld pool, the forming quality of the weld and the mechanical properties of the welded joint.
Taking welding current as an example, it is one of the most core parameters in the MIG welding process. The size of the welding current directly determines the depth and width of the welding pool, and then affects the permeability and forming quality of the weld. Generally speaking, with the increase of welding current, the depth of the weld pool increases, but too large current may lead to defects such as welding penetration and splashing. On the contrary, too small current may lead to problems such as welding impenetrability and poor weld formation. In actual operation, the optimal welding current range should be determined by testing according to the material, thickness and joint form of the aluminum alloy. For example, when welding 6063 aluminum alloy with a thickness of 6mm, the MIG welding process is used, and the current is usually set at about 170A to ensure the penetration and forming quality of the weld.
Welding voltage is also an important parameter that affects the welding quality of MIG. It determines the length and stability of the arc, which in turn affects the melting speed of the welding wire and the formation of the weld. The appropriate welding voltage should be matched with the welding current to ensure stable arc combustion and avoid unstable welding quality caused by voltage fluctuations. In practical applications, the choice of welding voltage also needs to consider the type and flow of protective gas. For example, when pure argon is used as a protective gas, the welding voltage can be appropriately reduced to save electric energy due to the high ionization energy of argon and good arc stability. At the same time, the flow rate of the protective gas also needs to be adjusted according to the welding current and nozzle aperture to ensure good protection and welding quality.
In addition, the welding speed and wire feed speed are also important factors affecting the quality of MIG welding. The welding speed determines the welding efficiency, and the wire feed speed determines the filling speed and the deposition efficiency of the welding wire. In actual operation, the selection of welding speed and wire feed speed should be comprehensively considered according to welding current, voltage and base material thickness. For example, when welding thicker aluminum alloy sheets, in order to obtain good penetration and forming quality, it is necessary to appropriately reduce the welding speed and increase the wire feed speed. At the same time, it is also necessary to pay attention to maintaining the coordination between the welding speed and the wire feed speed to avoid problems such as poor weld formation or welding defects.
Application of double pulse MIG welder in aluminum alloy welding
In the practice case of how to improve the quality and efficiency of MIG welding of aluminum alloy with double pulse MIG welding machine, we have to mention the lightweight body welding project of a well-known automobile manufacturer. In this project, the dual pulse MIG welder, with its unique current waveform control technology, significantly improves the mechanical properties and appearance quality of the welded joint. Specifically, by precisely regulating pulse frequency and duty cycle, the heat input in the welding process is fine controlled, and the width of the welding heat affected zone is effectively reduced, thus reducing the risk of welding deformation and residual stress. The data show that compared with the traditional MIG welder, the welding deformation of the double-pulse MIG welder in this project is reduced by about 30%, while the tensile strength of the welded joint is increased by about 10%.
In addition, the intelligent control system of the double-pulse MIG welder is also a key factor to improve welding efficiency. The system can monitor the current, voltage and other parameters in the welding process in real time, and automatically adjust the welding parameters according to the preset welding program to ensure the stability and consistency of welding quality. In the automotive manufacturer's welding line, the application of the double-pulse MIG welding machine has reduced the welding cycle by about 20%, greatly improving production efficiency. At the same time, the intelligent welding process monitoring and data analysis function also helps engineers to discover and solve potential welding quality problems in a timely manner, further improving the reliability of welding quality.
As welding technology experts said: "The emergence of the double pulse MIG welding machine is a revolutionary breakthrough in welding technology." It not only solves many problems faced by traditional MIG welders in aluminum alloy welding, but also provides us with a new way to improve welding quality and efficiency." This practical case fully demonstrates the great potential and broad application prospect of double pulse MIG welding machine in aluminum alloy MIG welding.
Unique advantages of a double pulse MIG welder
The unique advantages of double pulse MIG welding machine in the field of aluminum alloy welding are first reflected in its excellent welding quality control ability. By precisely regulating the double-pulse current waveform, the welding machine can significantly reduce the heat input fluctuations during welding, thereby effectively avoiding the performance degradation of aluminum alloy materials due to excessive heat affected zone. According to the experimental data, compared with the traditional MIG welding machine, the double-pulse MIG welding machine can reduce the width of the heat affected zone by about 20% when welding aluminum alloy, while increasing the tensile strength of the welded joint by about 15%. This advantage is particularly critical in the aerospace sector, where any slight welding defect can pose a threat to flight safety.
In addition, the intelligent control system of the double pulse MIG welding machine is also one of the highlights. The system can monitor various parameters in the welding process in real time, such as current, voltage, welding speed, etc., and automatically adjust according to the preset welding procedure to ensure the stability and consistency of welding quality. For example, in automotive manufacturing, lightweight welding practices require that welded joints have sufficient strength while maintaining a low weight. Dual-pulse MIG welders successfully achieve this goal by precisely controlling welding parameters, providing automotive manufacturers with efficient and reliable welding solutions. According to a well-known automobile manufacturer, after the use of double-pulse MIG welding machine, the quality of its aluminum alloy welding joint has increased by nearly 30%, while the production efficiency has also been significantly improved.
Therefore, the double pulse MIG welding machine with its excellent welding quality control ability, intelligent control system and excellent control ability of welding defects, in the field of aluminum alloy MIG welding has shown a unique advantage. These advantages not only improve the performance and quality of welded joints, but also promote the technological progress and industrial upgrading of related industries. As a famous welding expert said: "In the pursuit of efficient, high-quality welding today, double pulse MIG welding machine is undoubtedly the leader in the field of aluminum alloy welding."
So if you want to easily master the aluminum mig welding technology, you must have a high quality and excellent welding performance of the double pulse MIG welder. The Doughty MIG-285P double pulse MIG aluminum welder is an excellent aluminum welding device. It includes the characteristics and technologies of aluminum welding mentioned above, and is the first choice of aluminum welding leader in double pulse MIG welding machine on the market, and can also be used for teaching apprenticeship welder. Let's take a look at this one:
MIG-285P Double Pulse MIG Aluminum Welding Machine
Mig-285P double pulse aluminum MIG welding machine adopts the most advanced IGBT inverter technology, with excellent arc stability, advanced double pulse MIG welding technology, providing more stable and accurate welding results. This welder can easily handle aluminum and other metals, making welding easier and more efficient, ideal for welding aluminum and brass activities in the automotive industry. With an output power of 280 amps, this welder provides sufficient welding power to handle a wide range of projects. From automotive repair to manufacturing tasks, this welder provides precise and reliable welds that ensure strong and durable connections. The MIG-285P Liquid Crystal 280 AMP MIG welding machine is the solution of choice for all your welding needs. Whether you are a professional welder or an amateur welder, this welder will give you an amazing welding experience! This welder offers exceptional performance, versatility, and ease of use.
- New appearance design, LCD digital control panel
- 6 Functions in 1: Gas MIG welder,Gasless MIG welder Pulse MIG welder,Double Pulse MIG welder,Lift TIG welder and Stick welder. (TIG torch not included)
- MIG Synergistic & Manual Setting on MIG function, straightforward operation.
- Single pulse, double pulse optional, suitable for welding 0.8mm thin aluminum plate, carbon steel, stainless steel.Double pulse function, spatter-free welding, especially suitable for aluminum welding.
- Fast welding speed, small splash, deep weld pool, good weld formation;
- High load duration, efficiency is 3 times that of traditional argon welding, energy saving, high reliability.
- Permits visualization of welding process and parameters such as welding material, wire diameter, output voltage, and output current or wire feeding speed current.
- All metals can be welded: aluminum, stainless steel, carbon steel, low carbon steel, steel, iron, and cast iron.
This MIG-285P double pulse aluminum MIG welding machine is essential for heavy work! Industrial grade integrated trailer structure design, the smooth appearance of the styling design makes the machine look less bulky, and the external structure is more resistant to the collision of daily life. Whether you are sitting in the workshop or working outside, this durable TIG welder can be safely. The equipment is not sensitive to temperature and humidity, is stable throughout the year, and has no worries.

Doughty--Double pulse aluminum MIG welding
Each part is guaranteed to last at least 3 years, whatever you put it through. The welding unit and all included components come with a 1-year warranty, plus support 7 days a week from our team at crw@doughtywelder.com.
No matter what kind of welding machine and plasma cutting machine you need, it can meet your needs. If you need advice beyond what is provided in this article, please contact our sales team. Our team of experts can help you make the right choice.