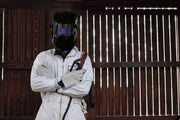
Understand the importance of welding techniques
Welding technology, as a process of melting and combining different materials through high temperature, is one of the indispensable key technologies in modern industrial production. It plays a vital role in many sectors including manufacturing, construction, automotive, aerospace and shipbuilding. According to statistics, the annual volume of welding operations in the world is up to hundreds of millions of tons, and the application of welding technology is wide, from household appliances used in daily life to complex spacecraft, which can not be separated from the support of welding technology.
For example, in automobile manufacturing, welding is a key technology to connect various parts of the body, which not only ensures the strength and safety of the automobile structure, but also plays a decisive role in improving production efficiency and reducing costs. In the field of construction, welding technology is used to connect steel structures, ensuring the stability and durability of buildings.
The accuracy and reliability of welding technology directly affect the overall quality, overall performance and service life of the product, therefore, mastering welding technology is not only the basis of industrial production, but also an important driving force to promote technological progress and innovation.As Einstein said: "Theory determines how high you can reach, practice determines how far you can go." In the study and practice of welding technology, understanding the principle and characteristics of various welding methods is very important to quickly grasp the shortcut of technology and practice.
Strategies for mastering welding skills quickly
1. Theoretical study: welding principles and safety knowledge
Welding technology is an ancient and progressive process based on the principle that metal materials melt and re-solidify at high temperatures to form permanent connections. In the welding process, the transfer of heat and the melting of materials are the core elements. For example, arc welding uses high temperatures (up to 6000°C) generated by an electric arc to melt metals, while laser welding uses a laser beam with a high energy density to melt and join materials. Understanding these basic principles is crucial to mastering welding techniques, as they determine the parameters set during the welding process, such as current, voltage, welding speed, and the flow of protective gases.
In the study of welding technology, safety knowledge can not be ignored. There are many potential hazards in welding operations, including electric shock, fire, harmful gases and radiation. According to the Occupational Safety and Health Administration (OSHA), welding is one of the leading causes of occupational injuries and illnesses. Therefore, welding personnel must be familiar with and follow safe operating procedures, such as using proper personal protective equipment (PPE), ensuring good ventilation conditions, and properly operating welding equipment. As Edison said: "Safety first, prevention is better than cure." In the field of welding, the implementation of preventive measures is the basis for ensuring personnel safety and welding quality.
2. Practical operation: basic welding skills and practice methods
In the process of learning welding technology, mastering basic welding skills is a crucial step. Basic welding techniques include key elements such as welding posture, arc control, electrode Angle and moving speed. For example, the correct welding posture can reduce fatigue and improve welding efficiency and quality. Arc control is the key to maintain stable arc in welding process, which directly affects the forming and quality of weld. The grasp of the Angle and moving speed of the electrode needs to be refined through a lot of practice to ensure that the weld is uniform and beautiful. In practice, beginners in welding can become familiar with these techniques through simulation exercises, such as straight line and arc welding exercises on scrap. In addition, referring to the teachings of welding masters, such as "Welding is a combination of science and art," can help learners understand that welding requires not only precise technique, but also a certain creativity and aesthetics.
Necessary welding tools and equipment
1. Selection and use of welding equipment
In the field of welding, choosing the right welding equipment is the key to ensure the quality and efficiency of welding. For example, gas shielded welding (GMAW) and tungsten electrode gas shielded welding (GTAW) are two common welding methods that are suitable for different materials and thicknesses respectively. Gas shielded welding machines are usually equipped with accurate wire feeding systems and gas flow controllers to ensure the stability of the welding process and weld quality. The tungsten gas welding machine requires high precision current control and stable arc to achieve high quality welding results. When selecting welding equipment, it is also necessary to consider its durability, maintenance costs and ease of operation. For example, some advanced welding equipment has a modular design that facilitates quick parts replacement and reduces downtime. In addition, the degree of intelligence of the equipment is also becoming higher and higher, for example, some welders are equipped with adaptive control technology, which can automatically adjust parameters according to real-time data during the welding process, thereby improving the consistency and reliability of the welding. In the selection and use of welding equipment, careful preliminary research and practical operation are also crucial to ensure that each step on the road to a quick introduction to welding technology is solid and powerful.
2. Welding auxiliary tools and their importance
In the field of welding, the use of auxiliary tools is essential to improve work efficiency, ensure welding quality and ensure safe operation. For example, the welding fixture can not only fix the workpiece, reduce welding deformation, but also improve the welding speed. According to statistics, the use of appropriate welding fixtures can increase the welding efficiency by more than 30%. In addition, personal protective equipment such as welding masks and protective clothing are essential tools to protect welders from UV rays, flying metal and harmful gases. In the process of quick introduction to welding technology, mastering the correct use of these auxiliary tools is one of the basic skills. As welding master Alexander de Hamm said, "A welder's skill is not only reflected in his welding technique, but also in his skillful use of tools and attention to safety." Therefore, the selection and use of welding auxiliary tools is an important content that welding technicians must deeply learn and practice.
At this point, you can choose DoughtyWelder, DoughtyWelder is a professional design and manufacture of the most advanced welding equipment, welding helmets and accessories, loved by people who love welding. Perfect for home and industrial use, you can find DoughtyWelder products worldwide and create inspiring and lasting work in people's hands.
A career path into the welding industry
1. Welding technician's daily work content
The daily work of a welding technician is multifaceted, involving the whole process from preparing for welding operations to completing welding tasks. They must be familiar with various welding methods, such as arc welding, gas shielded welding, laser welding, etc., and be able to choose the right welding technology according to different materials and project needs. For example, in the automobile manufacturing industry, welding technicians may need to use spot welding technology to join the steel plates of the body, which requires great accuracy and repeatability. According to the data of the International Welding Society, the error of the solder joint spacing and solder joint size must be controlled within 0.2 mm to ensure the integrity and safety of the structure.
In daily work, welding technicians also need to perform pre-welding preparation work, including checking welding equipment, preparing welding materials, cleaning welding surfaces, etc. They must ensure that the welding equipment is in good working condition to avoid production delays or safety incidents caused by equipment failures. The choice of welding material is also critical, for example, stainless steel welding requires the use of specific filling materials to prevent corrosion problems.
In addition, welding technicians need to constantly learn and adapt to new technologies in their daily work. With the development of Industry 4.0 and intelligent manufacturing, welding technicians may need to master robotic welding techniques, as well as the use of computer-aided design (CAD) and computer-aided manufacturing (CAM) systems for welding operations. As Henry Ford said, "If you do not progress, you regress." Welding technicians must continue to learn in order to keep their skills modern and competitive.
2. Career Development: The path from entry to specialist
In the field of welding, the promotion path from entry to becoming an expert is a road full of challenges and opportunities. Beginners usually start with basic welding techniques, such as learning basic operations such as arc welding and gas welding, and this step is the cornerstone of building welding skills. According to the American Welding Society (AWS), it takes about 1,000 hours of hands-on work to reach the level of a skilled worker. At this stage, welding technicians need to master welding principles, safety knowledge, and through continuous practice to improve welding quality and efficiency.
As their skills improve, welding technicians will begin to be exposed to more complex welding projects, such as using advanced welding equipment and materials, and performing welding operations in specific environments. For example, titanium alloy welding used in the aerospace industry requires technicians not only to have excellent welding skills, but also to understand the characteristics of the material and its impact on the welding process. At this stage, technicians can prove their professionalism by attending welding technical training and certification, such as obtaining a welding certificate from AWS.
As their careers progress to advanced levels, welding specialists need not only deep technical knowledge, but also the ability to innovate and solve complex problems. They may be involved in developing new welding technologies or improving existing processes to improve production efficiency and welding quality. For example, the development of laser welding technology has significantly improved the accuracy and speed of welding. In this process, experts need to keep an eye on industry trends and learn new technologies, such as reading professional journals and attending industry conferences, to maintain their competitiveness.
Ultimately, experts in the field of welding will be able to mentor and train a new generation of welding technicians, sharing their own experience and knowledge. They may take on the role of technical consultants or senior engineers involved in the development of welding standards and quality control processes. In the field of welding, the process of becoming an expert also requires unremitting effort and continuous learning.
Continuous learning and skill development
1. Participate in welding technical training and certification
In the process of welding technology training and certification, participants will have an in-depth understanding of the scientific principles of welding, and master the classification and characteristics of various welding methods, such as arc welding, gas shielded welding, resistance welding, etc. The training course usually includes two parts: theoretical study and practical operation. The theoretical part not only covers the welding principle, but also includes the safety knowledge in the welding process, so as to ensure that the students can comply with the safety norms in the actual operation and prevent accidents. In the practical operation part, through the practice of simulating the real working environment, students can master basic welding skills under professional guidance, such as electrode Angle, welding speed, welding pool control, etc. For example, the certification program offered by the American Welding Society (AWS) not only provides a systematic learning path for students, but also ensures that students have reached a certain level of skill through certification exams.
2. Keep an eye on industry trends and new technology developments
With the advancement of Industry 4.0 and the rise of intelligent manufacturing, welding technology is undergoing unprecedented changes. For example, laser welding technology is widely used in the automotive manufacturing and aerospace fields because of its high precision and high speed. According to the International Institute of Welding, the market share of laser welding has grown by nearly 20% in the past five years and is expected to continue to grow in the coming years. In addition, with the increasing emphasis on environmental sustainability, green welding techniques, such as cold metal transfer (CMT) welding, are gaining favor due to their low heat input and high efficiency. CMT welding technology not only reduces the consumption of materials and energy, but also significantly reduces the emission of harmful gases, which meets the requirements of modern industry for environmental protection. In terms of continuous learning and skill upgrading of welding technology, welding technicians need to constantly pay attention to the development of these new technologies and master these cutting-edge technologies by participating in professional training and certification courses in order to maintain their competitiveness in the industry.
Future trends in welding
1. New welding technology and material development
With the continuous progress of science and technology, the field of welding technology has also ushered in many innovations. New welding technologies such as laser welding, electron beam welding and friction stir welding are changing the traditional welding process. Laser welding technology is widely used in the automotive and aerospace industry with its high precision and high speed, for example, BMW uses laser welding technology on its production line to improve the strength and production efficiency of the body structure. Electron beam welding has found a place in the nuclear industry and aeroengine manufacturing for its deep penetration and high precision. In addition, with the development of materials science, the emergence of new welding materials such as nanomaterials and composite materials has brought new challenges and opportunities for welding technology. These materials not only improve the performance of welded joints, but also expand the application range of welding technology. For example, carbon nanotube-reinforced composites show great potential in improving the mechanical properties of welded joints. As Einstein said: "imagination is more important than knowledge", in the future development of welding technology, innovative thinking and the exploration of new materials will be the key to promote the progress of the industry.
2. The importance of green welding and sustainable development
With the enhancement of global awareness of environmental protection, green welding technology plays an increasingly important role in the field of welding. Green welding not only focuses on energy efficiency and material utilization in the welding process, but also emphasizes reducing the emission of harmful substances to achieve the goal of sustainable development. For example, the use of laser welding technology can significantly reduce the production of welding smoke and harmful gases, while improving the speed and accuracy of welding. According to the report of the International Institute of Welding (IIW), compared with traditional welding methods, laser welding can increase energy efficiency by more than 30%, and the material utilization rate can reach more than 95%. In addition, the negative impact on the environment can be further reduced through the use of environmentally friendly welding materials such as lead-free solder. As Einstein said, "The world of the future will not be the winners of weapons and wars, but of nations and nations that can solve environmental problems." Therefore, the welding industry must constantly explore and apply new technologies to ensure its long-term sustainability.