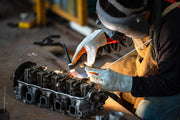
While welding ultra-thick and ultra-thin metals each presents their own unique challenges, many novice welders especially need help with thin sheets. Welding thin metals is challenging because there is a fine line between ensuring adequate penetration and avoiding burning holes in the weld. Even a small mistake can ruin an entire project.
Therefore, we present key tips for welding thin metals, delve into the unique challenges encountered when welding thin metals, and provide practical advice to help you overcome these challenges. These tips are designed to guide and support your welding learning journey.
1. Overview of the welding technique
1.1 Definition and importance of welding technology
Welding technology, as a process of melting metal materials through high temperature, is one of the indispensable key technologies in modern industrial production. It not only plays an important role in traditional manufacturing, such as the construction of ships, bridges, buildings and pipelines, but also plays a vital role in high-tech fields such as aerospace, automobile manufacturing and electronic equipment. According to the International Institute of Welding (IIW), the application of welding technology can improve the material utilization rate by up to 60% and significantly reduce the cost of materials. In addition, advances in welding technology have driven the development of material science, for example, by accurately controlling the thermal input during the welding process, thus improving the mechanical properties and corrosion resistance of components. As American inventor and engineer Charles Kettlin puts it, " Innovation is the combination of old elements in new ways."Welding technology is the embodiment of this innovative spirit, through continuous technological innovation, it combines a variety of metal materials in new ways, for the progress of human society to provide a solid technical support for the future.
1.2 Common application fields of metal sheet welding
Metal sheet welding technology plays a vital role in modern industry, especially in automotive manufacturing, aerospace, ship construction and building structure. For example, in automobile manufacturing, thin metal sheet welding is used for the assembly of the body, which not only requires the welding point to be beautiful and high strength, but also must meet the requirements of lightweight and cost effectiveness. According to statistics, welding work accounts for more than 30 percent of the total manufacturing time in the manufacturing process of a modern car. In the field of aerospace, welding technology ensures the integrity and safety of the aircraft structure. For example, in the manufacturing of Boeing 787 Dreamliner, a large number of advanced metal sheet welding technology is used to build its light, high strength body structure. These applications not only demonstrate the diversity of metal sheet welding technologies, but also demonstrate their importance in improving production efficiency, reducing costs, and enhancing product performance.
2. Preparation work before welding
2.1 Select the appropriate welding equipment and materials
In the metal sheet welding technology, choosing the appropriate welding equipment and materials is the key to ensure the welding quality and efficiency. The selection of welding equipment shall be based on the welding method, the nature of the workpiece material, and the production requirements. For example, for the welding of stainless steel sheet, TIG (tungsten pole argon arc welding) welder is generally considered preferred due to its stable arc and high quality weld. TIG welders can accurately control welding parameters, such as current, voltage and welding speed, which is particularly important for sheet welding, which is very sensitive to thermal input and easy to produce deformation or burn through.
In terms of material selection, the chemical composition of the welding filling material must match the base material to ensure the mechanical properties and corrosion resistance of the weld joint. For example, when welding the aluminum alloy sheet, the welding wire similar to the base material alloy composition should be selected to avoid the strength decrease or the crack in the weld area. In addition, the choice of welding wire diameter is also crucial, which affects the welding speed and weld formation. Usually, a thinner wire is suitable for sheet welding because it reduces thermal input and reduces the risk of workpiece deformation.
In practical applications, the choice of welding equipment and materials should also consider the welding environment and cost-effectiveness. For example, the use of robotic welding systems can improve the consistency of production efficiency and welding quality, especially in mass production, which has a high ROI. However, for small batch or custom production, manual welding may be more economical. In the selection of welding equipment and materials, the welding quality should always be the premise, and then the cost benefit should be considered.
2.2 Surface treatment of metal sheet before welding
In the metal sheet welding technique, the surface treatment is one of the key steps to ensure the welding quality. Surface treatment can not only remove oil, oxides and impurities from the metal surface, but also improve the performance of welded joints. For example, before TIG (tungsten argon arc welding) welding, the metal sheet is usually pickling or sandblasted to remove the oxide layer of the surface to obtain a cleaner and more uniform welding surface. According to the ASTM standard, the concentration and treatment time of the pickling solution need to be strictly controlled to avoid decreased material properties due to excessive corrosion. Furthermore, surface treatment involves polishing the metal surface to achieve the required roughness, which helps to improve the mechanical bite strength of the weld. In some cases, such as in the aerospace field, the surface treatment before welding is extremely strict, and even needs to be performed in a clean room environment to ensure the absence of dust and other pollutants. Therefore, the proper surface treatment of metal sheet is an indispensable link to achieve high quality welding.
3. Foundation of the welding process
3.1 Classification and characteristics of the welding process
The classification and characteristics of sheet metal welding technology are the crucial basic knowledge points in the field of welding technology. According to different classification standards, the welding process can be divided into various types, such as heat source can be divided into arc welding, resistance welding, laser welding, etc.; according to the melting pool protection method can be divided into gas protection welding, self-protection welding, etc. Each welding process has its own unique characteristics and scope of application. For example, gas protection welding, such as carbon dioxide welding, is widely used in the welding of thin metal plates because of its low cost, fast welding speed and strong adaptability. However, it is sensitive to the wind speed and needs to be operated in a windless or breezy environment to avoid the protective gas being blown away and affecting the welding quality. In practical application, the selection of appropriate welding process needs to comprehensively consider the nature, thickness, joint form and production efficiency of the materials. For example, for aluminum alloy sheets, TIG welding (tungsten-based argon arc welding) is preferred because of its ability to provide a high-quality weld, although relatively slowly. In the development process of welding technology, the innovation and optimization of welding process is always the key to promote the progress of the industry. A deep understanding of the classification and characteristics of various welding processes is of inestimable value for improving the welding quality, optimizing the production process and reducing the cost.
3.2 Common welding methods of metal sheet welding
Metal sheet welding is one of the indispensable processes in the modern manufacturing industry, which requires the welding personnel to have the ability to accurately control the welding parameters to ensure the welding quality. Among many welding methods, gas protection welding (such as TIG and MIG welding) is widely used in metal sheet welding because it can provide high quality welds.
For example, TIG welding (tungsten-inert gas protection welding) is particularly suitable for sheet materials because it enables fine control and low thermal input, thus reducing material deformation and thermal impact zone. In practice, TIG welding can reach a minimum weld width of 0.01 inches (about 0.25 mm), which is particularly important for aerospace parts that require extremely high precision.
Smaller diameter tungsten electrodes are recommended for TIG welding of thin sheets. These electrodes can adapt to the low current start required for thin metal materials and effectively protect tungsten tips when welding steel. With ER70S-2 or silicon bronze filler rods, excellent welding results can be achieved on thin sheets.
No matter which welding technology you prefer, we highly recommend that you choose a TIG welder with pulse function. The DoughtyWelder TIG200P AC/DC model, with its low current output, pulse function and AC/DC selectivity, meets most thin metal welding needs and is suitable for a wide range of metal materials including steel, stainless steel and aluminum.
In addition, MIG welding (metal inert gas protective welding) is also commonly used in mass production of thin plate welding operations due to its simple operation and fast welding speed. In the field of automobile manufacturing, MIG welding has become the key technology for body assembly due to its high efficiency and good weld forming ability. In order to further improve the welding quality, the setting and adjustment of the welding parameters must be based on a deep understanding of the material characteristics and the welding environment. For example, a precise match of welding speed, current, and voltage is essential to obtain defect-free welds. The control of the thermal input is particularly critical during welding, because it leads to the thermal deformation of the metal sheet and the embrittlement of the weld. Therefore, the welding operator needs to carefully select and adjust the welding parameters according to the heat conduction characteristics, thickness and welding position of the material. To master the skills of metal sheet welding requires the welding personnel to have rich experience, exquisite skills and a deep understanding of welding science.
4. Welding skills and operation key points
4.1 Setting and adjustment of welding parameters
During the welding process of metal sheet, the setting and adjustment of welding parameters are the key factors to ensure the welding quality. Welding parameters include current, voltage, welding speed, gas flow, etc. The precise control of these parameters directly affects the formation of weld seam, melting depth, the size of thermal influence area and the generation of welding defects. For example, when using gas protection welding (e. g. MIG / MAG welding), the matching between current and voltage is essential to obtain a stable arc and good weld forming. Historically, the current to voltage ratio is usually maintained in the range of 20:1 to 25:1 to ensure the stability of the welding process and the quality of the weld. In addition, the adjustment of welding speed must be matched with the welding heat input, too fast may cause the weld cooling too fast, unfusion or crack; too slow may lead to excessive heat input, increase the width of the thermal influence area, and affect the mechanical properties of the material. In practice, the setting of welding parameters often needs to be combined with the nature, thickness and welding location and other factors. For example, when welding thin aluminum plates, lower welding speed and increased heat input may be required to ensure adequate fusion. Meanwhile, the adjustment of welding parameters shall also follow the relevant welding standards and specifications, such as the guidelines provided by AWS (American Welding Society) or ISO (International Organization for Standardization). Through precise parameter setting and adjustment, welding operators can effectively control the welding process, improve the welding efficiency and quality, so as to achieve a leap from basic to proficient in the field of metal plate welding.
4.2 Thermal input control during the welding process
Thermal input control is one of the key factors of ensuring the welding quality. The amount of heat input directly affects the weld microstructure, mechanical properties, and the degree of welding deformation. For example, in the welding of mild steel, the heat input is usually controlled in the range of 0.5 to 2.5 kJ / mm to avoid the problem of increased brittleness or large grain size. In order to accurately control the thermal input, welding engineers will use thermal simulation technology to simulate the thermal cycle during the welding process and predict the temperature distribution and cooling rate of the weld area. In addition, the precise adjustment of welding speed, current and voltage is also an important means to achieve thermal input control.
5. Welding industry standards and regulations
5.1 Introduction and interpretation of welding standards at home and abroad
In the field of metal sheet welding, following the domestic and foreign welding standards is the key to ensure the welding quality and safety. For example, the standards issued by the International Institute of Welding (IIW) provide uniform guidance for global welding practices, while the American Institute of Welding (AWS) standards are widely used in North America. In Europe, the standards set by the European Standardization Committee (CEN) such as EN ISO 9606-1 set strict requirements for the qualification of welding personnel. These standards not only cover the setting of welding materials, welding methods and welding process parameters, but also include the detailed provisions of welding quality control and inspection. For example, the requirements of the welding quality system provide a framework for the quality assurance of welding products. In practical application, the welding engineer must have a deep understanding and accurate interpretation of these standards to ensure that the welding work meets the regulatory requirements, while meeting the customer's expectations of product quality. For example, a study of the automotive industry showed that a welding process meeting ISO 3834 standards reduced the welding defect rate by 30%, significantly improving product reliability and safety. Therefore, the mastery of welding technology is not only reflected in the mastery of welding skills, but also reflected in the deep understanding and strict implementation of welding standards.
5.2 Laws and regulations related to welding operation
In welding operations, compliance with the relevant legal and regulatory requirements is the cornerstone of ensuring the safety and quality of the operations. For example, the U. S. Occupational Safety and Health Administration (OSHA) stipulates that welding operations must be conducted in well-ventilated environments to reduce the threat to workers' health of harmful gases and smoke. According to OSHA standard 29 CFR 1910.1000, the concentration of air pollutants in the welding area shall not exceed the allowable limit value, which requires enterprises to must regularly test the air quality and take necessary ventilation measures. In addition, the maintenance of welding equipment must follow the manufacturer's guidance and relevant national standards, such as the American Association of Materials and Testing (ASTM) standards, to ensure the normal operation and welding quality of the equipment. At the international level, the International Welding Society (IIW) has also issued a number of guidance documents designed to promote the standardization and safety of welding operations worldwide. For example, IIW's Welding and Cutting Safety Guide provides a comprehensive safe operation framework for welding operations. In practice, the compliance of welding operations is not only related to enterprise compliance, but also to respect and guarantee the safety of employees,
6. Application of welding technology in specific industries
6.1 Welding technical requirements in the aerospace field
In the field of aerospace, the application requirement of welding technology is extremely strict, because it is directly related to the safety and reliability of the aircraft. For example, the combustion chamber of the rocket engine and the thermal protection system of the space shuttle, which operate at extreme temperature and pressure, require the strength, corrosion resistance and fatigue resistance of the welded joints. According to NASA research, welding defects are one of the main causes of spacecraft failure, so the quality control during the welding process is crucial. In the education and training of welding technology, special emphasis is placed on the professional curriculum of welding technology in these demanding fields to ensure that welding engineers can master the necessary theoretical knowledge and practical skills. The importance of practical operation and skill certification is particularly prominent in the aerospace field, because the success of every flight mission is based on the perfection of every welding point.
6.2 Application of welding technology in automobile manufacturing
In the field of automobile manufacturing, the application of welding technology is the key link to ensure the vehicle structural strength and safety. According to statistics, a modern car requires about 3,000 to 5,000 solder joints that hold all the parts of the body firmly together. With the increasing requirements of lightweight and energy saving and emission reduction in the automobile industry, the importance of metal sheet welding technology in automobile manufacturing is becoming more and more prominent. For example, the use of aluminum alloy and high-strength steel not only improves the fuel efficiency of the automobile, but also puts forward higher requirements for the welding process. In this context, precise control of welding parameters, such as current, voltage, and welding speed, becomes crucial. Moreover, thermal input control during welding is essential to prevent material performance degradation and avoid the generation of thermal cracks. Therefore, automobile manufacturers must adopt advanced welding technology to ensure that every vehicle meets strict quality standards.
7. Advanced Welding skills and innovative applications
7.1 Challenges and countermeasures of welding technology for special materials
In the metal sheet welding technology, the welding technical challenge of special materials is particularly prominent, which not only requires the welding engineers to have deep professional knowledge, but also requires them to master advanced welding skills. For example, special materials such as titanium alloy and high-strength steel are prone to crack and stress concentration during the welding process, which requires that the welding parameters must be set precisely to ensure the strength and toughness of the welded joints. According to the International Institute of Welding (IIW), small changes in welding parameters may cause significant differences in welding quality. Therefore, the setting and adjustment of welding parameters should be comprehensively considered according to the material characteristics, welding methods and welding environment.
In practice, the welding engineers will usually use the measures such as preheating and post-heat treatment to control the heat input and reduce the welding stress and deformation. For example, for titanium alloy materials, the preheating temperature is usually controlled between 150°C and 200°C to reduce the thermal sensitivity of the material. In addition, the pulse current technology used in the welding process can effectively control the thermal input, reduce the width of the thermal influence area, thus improving the welding quality.
In view of the challenge of welding of special materials, the innovative application of welding technology is also particularly important. For example, laser welding technology is widely used in the aerospace field because of its high energy density and precise control ability. According to NASA research, laser welding technology can achieve precision welding of special materials such as titanium alloy, significantly improving the performance and reliability of structural parts. At the same time, with the development of digital welding technology, the real-time monitoring and quality control of the welding process has become more accurate, which provides a new solution for special materials welding.
In conclusion, the challenge of welding technology for special materials requires welding engineers to constantly learn and master new technologies, and at the same time, to ensure that welding quality meets the growing industrial needs through scientific analytical models and strict quality control processes.
7.2 Application prospect of welding technology in emerging fields
With the advent of industry 4.0 era, the application prospect of welding technology in the emerging fields has become particularly broad. For example, in the manufacturing of new energy vehicles, welding technology is the key process to connect the battery module, frame and body, and its accuracy and efficiency directly affect the performance and safety of the product. According to the International Energy Agency (IEA), the global sales of new energy vehicles will reach 58 million units by 2030, which will bring huge market demand for welding technology. In the aerospace field, as the demand for lightweight and high-strength materials increases, welding technology plays an important role in the connection of titanium alloy, aluminum alloy and other materials. For example, both Boeing and Airbus have heavily used advanced laser welding technology in their latest models to improve structural reliability and reduce aircraft weight. In addition, with the integration of digital and intelligent technology, welding technology is gradually realizing automation and intelligence, which not only improves the welding quality, but also reduces the labor cost. For example, by introducing machine vision and artificial intelligence algorithms, the welding robot can automatically identify the welding defects and adjust them in real time, thus ensuring the stability and consistency of the welding process. These technological advances and application cases show that the application prospect of welding technology in the emerging fields is not only broad, but also is becoming an important force to promote industrial progress and innovation.
7.3 Development and application of green welding technology
With the enhancement of global awareness of environmental protection, the development and application of green welding technology has become an important trend in the welding industry. Green welding technology not only focuses on the efficiency and quality of the welding process, but also emphasizes on reducing energy consumption, reducing the emission of harmful substances and improving material utilization. For example, the laser welding technology can significantly reduce the production of heat input and welding smoke, while improving the welding speed and accuracy. According to the International Institute of Welding, laser welding technology can reduce energy consumption by up to 50% in some applications, and can reduce material waste by more than 30% due to its high precision characteristics. In addition, green welding technologies include the use of environmentally friendly welding materials, such as lead-free solders, and the development of waste recycling and reuse systems during the welding process. In practice, some advanced enterprises have begun to implement the digital management of the welding process, through real-time monitoring of welding parameters and environmental impact, optimize the welding process, reduce the waste of resources. The development of green welding technology is the embodiment of this combination, which not only promotes the progress of welding technology, but also makes a contribution to the realization of the goal of sustainable development.
No matter what kind of welding machine you need, Doughty Welder can provide for your needs. Contact our sales team if you need advice beyond what this article provides. Our team of experts can help you make the right choice.
🧐🧐🧐You might like the following:
1.The historical evolution of welding technology: from ancient processes to modern innovations
2. Holiday welding skills learning best practices stainless steel welding
3.Based on 4000+ customer reviews, this plate gold welding artifact stan