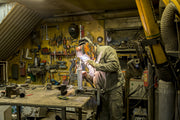
1. Introduction to stainless steel welding
1.1 Characteristics of stainless steel materials
Stainless steel materials, with their excellent corrosion resistance, high strength, and aesthetic properties, hold a significant position in numerous industrial applications and are widely used in industries such as construction, medical, and food processing. For example, 304 stainless steel contains 18% chromium and 8% nickel, and this alloy composition endows it with outstanding corrosion resistance, allowing it to maintain structural integrity and surface finish even in harsh environments. During welding, these characteristics of stainless steel require precise welding techniques to avoid thermal deformation and welding defects such as cracks and porosity, which can severely affect the materials corrosion resistance and overall strength. The selection and application of welding techniques must take into account the thermal expansion coefficient of stainless steel to ensure the stability and long-term durability of the weld joint.
1.2 The role of welding in stainless steel processing
In the field of stainless steel processing, welding technology plays a crucial role. As the primary means of connecting stainless steel components, welding not only ensures structural integrity but also enhances the overall performance of products. For instance, in the construction industry, stainless steel welding is used for supporting structures and decorative elements, and its improved corrosion resistance means that buildings can withstand harsh weather and pollution, extending their lifespan. In medical device manufacturing, welded stainless steel components must meet strict hygiene standards to ensure cleanliness and sterility of the equipment. Proper application of welding technology, such as laser welding, can achieve almost defect-free seams, which is essential for the cleaning and sterilization of medical devices. Additionally, welding can enhance the strength and durability of stainless steel structures, which is particularly important for industrial applications subjected to high loads. For example, in food processing equipment, welded stainless steel components must withstand repeated cleaning and sterilization processes, and optimized welding technology can significantly improve the lifespan and reliability of these components.
2. Advantages of stainless steel welding
2.1 Improvement of corrosion resistance
The application of stainless steel welding technology has significantly enhanced the corrosion resistance of materials, which is crucial for equipment and structures operating in harsh environments. For example, in the chemical industry, stainless steel welded pipes and vessels can resist the erosion of strong acids and strong alkalis, ensuring the safety of production processes and the purity of products. According to ASTM A240 standards, stainless steel materials can withstand up to 1000 hours of salt spray testing without showing signs of corrosion under specific conditions, which is particularly evident in performance comparisons before and after welding. Welding techniques such as TIG welding (GTAW) and MIG welding (GMAW) provide uniform and dense weld seams while significantly reducing the risk of localized corrosion caused by improper welding. Stainless steel welding achieves a leap in corrosion resistance by optimizing material structure.
2.2 Compliance with aesthetic and hygiene standards
In the field of stainless steel welding, meeting aesthetic and hygiene standards is crucial. Stainless steel materials, due to their smooth surfaces and excellent corrosion resistance, are widely used in industries such as food processing, medical equipment, and architectural decoration. For example, kitchen equipment manufacturers typically use 304 or 316 grade stainless steel because these materials not only have good corrosion resistance but also provide surfaces that meet hygiene standards, reducing the likelihood of bacterial growth. According to guidelines from the World Health Organization, the roughness of stainless steel surfaces should be less than 0.8 micrometers to ensure easy cleaning and disinfection. During welding processes, appropriate welding techniques, such as TIG welding (GTAW) , can minimize weld seam width and roughness, thereby achieving both aesthetic and hygiene standards. As the architectural master Louis Sullivan put it: "Form follows function," the aesthetics of stainless steel welding are not only reflected in its appearance but also in its functionality and hygiene safety.
2.3 Strengthening of strength and durability
The continuous advancement of stainless steel welding technology has significantly improved the strength and durability of welded stainless steel structures. For example, in the construction industry, stainless steel welded components can withstand tensile strength up to 550 MPa, which is much higher than that of ordinary steel. This high strength characteristic makes stainless steel welded structures particularly outstanding when subjected to heavy loads and harsh environments. In terms of durability, the application of stainless steel welded components in marine environments demonstrates that their corrosion resistance can last for several decades, thanks to the excellent corrosion resistance of stainless steel materials and the refined processing techniques of welding. In industrial applications, stainless steel welded pipes and containers, through precise control of welding parameters and the use of advanced welding technologies such as laser welding, can achieve almost defect-free weld joints, ensuring long-term sealing and structural integrity. The progress in enhancing structural strength and durability through stainless steel welding undoubtedly provides a solid quality guarantee for the long-term development of related industries.
3. Disadvantages of stainless steel welding
3.1 Thermal deformation problem in welding process
During the welding process of stainless steel, thermal deformation is an issue that cannot be ignored, as it directly affects the dimensional accuracy and structural integrity of the welded piece. Due to the high thermal conductivity of stainless steel, the heat generated during welding will rapidly spread, causing thermal expansion of the welding area and its surroundings. For example, in TIG welding (GTAW) welding, the temperature in the welding area can reach over 1000°°C, which is sufficient to cause significant thermal deformation. According to research, the thermal expansion coefficient of stainless steel during welding is approximately 10^-6/°C to 15^-6/°C, meaning that for every increase of 100°°C, the material length increases by 0.01% to 0.015%. This slight dimensional change can have a significant impact in precision engineering, such as misalignment of joints in pipeline systems, thereby affecting the overall sealing and safety of the system.
To control thermal deformation, welding engineers typically employ various strategies such as preheating, segmental welding, and fixture clamping. Preheating can reduce the temperature difference between the welding area and the surrounding material, thereby decreasing thermal stress and deformation. Segmental welding involves welding in stages, allowing the welding area sufficient time to cool down and reducing heat accumulation. Fixture clamping can effectively secure the welding piece, preventing displacement caused by thermal expansion. In some cases, engineers also use computer simulation techniques, such as finite element analysis (FEA), to predict thermal deformation during welding and design welding sequences and fixture layouts accordingly to minimize deformation.
The resolution of thermal deformation issues is not only related to welding quality but also closely associated with cost and production efficiency. For example, excessive thermal deformation can lead to additional correction work or even scrapping of the welded piece, which undoubtedly increases production costs. Therefore, by optimizing welding process parameters and adopting advanced welding technologies such as laser beam welding or electron beam welding, it is possible to minimize thermal deformation while maintaining high production efficiency. As a famous saying in the welding field goes: "Welding is not only an art of connecting metals but also a science of controlling thermal deformation."
3.2 Generation and influence of welding defects
In the welding process of stainless steel, the generation of welding defects is one of the inevitable challenges. Welding defects not only affect the aesthetics of the structure but more importantly, they significantly reduce the mechanical properties and corrosion resistance of welded components. For example, cracks are one of the most serious defects in welding, which can lead to sudden fracture of the material when subjected to load. According to a study, the generation of welding cracks is closely related to the thermal expansion coefficient and cooling rate of the welding material. In stainless steel welding, if the welding speed is too fast or the heat input is too large, the stress generated during material cooling exceeds its yield strength, which may result in cracks. In addition, porosity defects are also common problems, which reduce the effective load-bearing area of the weld seam, thereby decreasing the overall strength of the structure. In some cases, the presence of porosity can also become a source of corrosion, accelerating material damage. Therefore, the identification and prevention of welding defects are key aspects to ensure the quality of stainless steel welding.
3.3 Technical requirements
The technical requirements for stainless steel welding are a significant challenge in this field.Stainless steel welding imposes higher demands on the skill levels of operators.Welders not only need to have solid theoretical knowledge but also must master various welding techniques through prolonged practice.For example,TIG welding(GTAW) requires welders to accurately control welding speed,arc length,and the addition of filler materials to ensure weld quality.According to the standards set by the International Welding Institute (IIW),welders typically need professional certification to qualify for relevant work.This high demand for specialized skills undoubtedly increases the human resource costs for enterprises.
Driven by technological advancements, the stainless steel welding field continues to see the emergence of new solutions to address high costs and technical challenges. For example, the application of automation and robotic welding technologies, although requiring significant initial investment, can improve production efficiency and reduce human errors over the long term, thereby lowering overall costs. Meanwhile, with the integration of Computer-Aided Design (CAD) and Computer-Aided Manufacturing (CAM) technologies, the simulation and optimization of welding processes have become more precise, which helps reduce material waste and improve welding quality. In the stainless steel welding field, high-quality welding outcomes often mean less rework and maintenance, thus saving costs in the long run.
4. Selection of stainless steel welding technology
4.1 Overview of commonly used stainless steel welding technology
Stainless steel welding technology is an indispensable part of modern industry, playing a crucial role in enhancing material corrosion resistance, meeting aesthetic and hygiene standards, as well as strengthening structural strength and durability. Among various welding techniques, TIG welding (GTAW) and MIG welding (GMAW) are the most commonly used methods. TIG welding is renowned for its high-quality welds and good adaptability to thin materials, making it particularly suitable for fields with extremely high hygiene and strength requirements, such as food processing, medical equipment, and aerospace. For example, TIG welding can achieve almost seamless welding, which is essential for the manufacture of precision components. On the other hand, MIG welding is widely used in the automotive and construction industries due to its fast welding speed, ease of operation, and strong adaptability. However, each technology has its limitations; for instance, MIG welding may cause overheating and deformation when welding thin stainless steel materials. Therefore, when selecting a welding technique, it is necessary to consider factors such as material thickness, welding position, production efficiency, and cost to ensure a balance between welding quality and economic benefits.
4.2 Applicable scenarios and advantages and disadvantages of each technology
In the selection of stainless steel welding techniques, different welding methods are suitable for various application scenarios and each has its unique advantages and disadvantages. For example, gas shielded welding (such as TIG and MIG welding) is very popular in situations requiring high-quality welds and precise control, especially in food processing and medical device manufacturing, due to its ability to provide clean, spatter-free welding results. However, gas shielded welding is relatively more expensive and has higher technical requirements for operators. In contrast, stick welding (such as SMAW) is widely used in construction and heavy industry due to its lower equipment costs and ease of operation, although it may not be able to provide as consistent high-quality welds as gas shielded welding.
When selecting welding techniques, it is essential to consider the issue of thermal deformation during the welding process. For example, laser welding technology excels in controlling heat input, capable of minimizing heat-affected zones and reducing deformation, which is particularly important in the manufacturing of precision components. However, laser welding equipment is expensive and requires extremely high standards for surface treatment and assembly accuracy of the workpiece. In some cases, traditional stick electrode stick welding (SMAW) may be more economical, although it is less precise than laser welding in terms of controlling thermal deformation. Therefore, when choosing a welding technique, factors such as cost, accuracy, and production efficiency must be weighed.
The best practices for stainless steel welding emphasize preparatory work before welding and quality control during the welding process.For example, cleaning work before welding is crucial because any oil, grease, or oxide can lead to welding defects.In some cases, using pre-treatment methods such as acid washing or blasting can significantly improve welding quality.During welding, adopting appropriate welding parameters and continuous monitoring of welding quality is key to ensuring weld strength and durability.For instance, precise control of welding current, voltage, and welding speed can reduce welding defects such as cracks, porosity, and lack of fusion.Furthermore, appropriate heat treatment after welding, such as annealing, can relieve stress and enhance the overall structural stability.
5. Best practices for stainless steel welding
5.1 Preparations before welding
During the preparation stage of stainless steel welding, ensuring welding quality hinges on thorough cleaning of the welding surface and appropriate material processing. The oxide layer and impurities on the stainless steel surface must be thoroughly removed to prevent the generation of welding defects such as porosity and inclusions. For example, according to ASTM A380 standards, the cleanliness of the stainless steel surface should reach a level where there are no visible oils, greases, oxide scales, rust, or other foreign substances. In practice, this is typically achieved through methods such as mechanical grinding, chemical cleaning, or electrochemical polishing. Additionally, material preparation before welding includes precise measurement and marking of the weld area to ensure the accuracy of the welding position, thereby improving welding efficiency and quality. Pre-welding preparations not only require meticulous operation but also necessitate that welders possess extensive experience and a deep understanding of material properties, as welding master Alexander de Robinson said: "Welding is not just a technique, it is an art."
5.2 Quality control points in welding process
In the stainless steel welding process, quality control is a critical aspect to ensure the performance of the welded joint. Pre-welding preparations such as material cleanliness, calibration of welding equipment, and the qualifications of welding personnel all directly impact welding quality. For example, it must be ensured that the stainless steel surface is free of oils, oxides, and other contaminants before welding, as these impurities can reduce the corrosion resistance of the weld seam. According to ASTM A380 standards, the cleanliness of the stainless steel surface should reach Grade 2B to ensure welding quality. During welding, temperature control is another important factor. When welding stainless steel, controlling the heat input is crucial; excessive heat input can lead to coarse grain size, thereby reducing the strength and corrosion resistance of the weld seam. Therefore, appropriate welding speed and current should be used during welding to maintain an appropriate heat input. Additionally, the choice of welding technology is also crucial for quality control. For instance, TIG (Tungsten Inert Gas) welding is widely used in demanding applications due to its ability to provide high-quality weld seams. During welding, welding process specifications such as AWS D1.6 standards should be followed to ensure that welding parameters such as current, voltage, and welding speed meet the specified requirements. Post-welding inspection and testing of the weld seam are also important aspects of quality control. Non-destructive testing techniques such as X-ray inspection, ultrasonic inspection, etc., are employedMagnetic particle inspection can be used to evaluate the integrity of weld joints. The control of welding quality not only relates to the performance and life of products but also directly affects the economic benefits and market competitiveness of enterprises. As welding master Eugene F. Lauer said: "Welding quality is the soul of welding work, without quality there is nothing."
6. the future trend of stainless steel welding
6.1 Development of new welding technology
With the continuous advancement of technology, the development of new welding techniques has brought about revolutionary changes in the field of stainless steel welding. For example, laser welding technology has been widely applied in stainless steel welding due to its high precision and high speed. According to a study, laser welding can achieve welding speeds up to 1000mm/s while maintaining the uniformity and strength of the weld seam, significantly improving production efficiency and product quality. In addition, electron beam welding technology can achieve welding with almost no heat-affected zone when processing ultra-thin stainless steel materials, which is crucial for maintaining the original properties of the material. In terms of environmental protection, the emergence of cold metal transfer (CMT) welding technology not only reduces heat input and deformation during welding but also significantly reduces the generation of welding fumes, meeting the requirements of modern industry for environmental protection and energy conservation. New welding technologies are precisely the re-examination and innovation of traditional welding methods, which not only improve the efficiency and quality of stainless steel welding but also point out the direction of sustainable development for the welding industry.
6.2 Application prospect of environmental protection and energy saving in welding
With the increasing global emphasis on environmental protection and energy conservation, the stainless steel welding industry is actively seeking more environmentally friendly and energy-saving solutions. For example, laser welding technology, due to its high efficiency and low energy consumption, is gradually becoming one of the preferred technologies in industrial welding. According to relevant research, compared with traditional welding methods, laser welding can improve energy efficiency by more than 30%, while reducing material waste and harmful gas emissions. In addition, with the development of digital and intelligent technologies, the automation and intelligence levels of the welding process are also improving, which not only enhances welding quality but also further reduces energy consumption and material waste. For instance, by introducing advanced welding robots and intelligent control systems, precise control over welding parameters can be achieved, thereby reducing unnecessary energy consumption. As dison said: "The success of the future depends on the measures we take today," in the field of stainless steel welding, the practices of environmental protection and energy conservation are not only crucial for the sustainable development of enterprises but also a positive response to social responsibility.
🧐🧐🧐You might like the following:
1.Quick Start Guide for the welding industry: A shortcut to mastering te
2. DoughtyWelder MTC-215 5-in-1 Multi-Functional Welder Cutter User Guide
3.The historical evolution of welding technology: from ancient processes
No matter what kind of welding machine you need, Doughty Welder can provide for your needs. Contact our sales team if you need advice beyond what this article provides. Our team of experts can help you make the right choice.