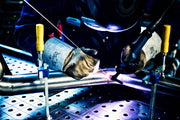
Tungsten Inert Gas Welding (TIG welding for short), also known as gas tungsten arc welding (GTAW), is a non-molten gas shielded welding technology. Argon gas is used as a shielded gas to melt the base metal and fill the welding wire through the arc generated between the tungsten electrode and the workpiece. It is commonly used in industries such as aerospace, automotive and manufacturing, where accuracy and reliability are critical. The control provided by TIG welding makes it ideal for both thin and thick materials, and is often the first choice for projects requiring the highest process standards.
Characteristics of TIG welding
1. Excellent protection performance: Argon is an inert gas, can effectively isolate the air, prevent weld metal oxidation, suitable for all kinds of metal materials welding.
2. Can achieve high current density welding: arc heat concentration, suitable for high current density welding, can achieve high quality welded joints.
3. Open arc welding: The welding process is visible, easy to observe the weld pool, which is conducive to the welding of single-side welding and double-side forming.
4. Stable welding process: stable arc combustion, no splash, beautiful weld formation.
5. Wide range of application: suitable for welding of all kinds of metals and various spatial positions, including welding of ultra-thin parts.
DC reverse welding shall not be used for welding
The heat output of the anode is much higher than that of the cathode in DC argon tungsten arc welding, so when DC positive welding (workpiece positive) is used, the tungsten electrode is not easy to overheat due to small heat output, and the tungsten electrode of the same diameter can use a larger current. At this time, the workpiece heat is large, the depth of penetration is also large, the productivity is high, the tungsten electrode hot electron emission capacity is stronger than the workpiece, so that the arc is stable and concentrated. Therefore, most metals (except aluminum, magnesium and their alloys) should be welded with direct current welding. DC reverse welding is the opposite of the above, and is generally not recommended.
a: DC reverse connection b: DC positive connection
Tungsten electrode ends cannot use sharp cone angles
When the welding current is large, the fine diameter sharp cone angle tungsten electrode is used, which will make the current density too large, resulting in overheating and melting of the tungsten electrode end and increasing burn loss. At the same time, the arc will also extend to the end of the tungsten pole, so that the arc column will obviously expand, drift unstable, and affect the weld formation. Therefore, when the high current welding, the thicker diameter tungsten pole should be selected, and its end should be ground into a blunt cone angle or flat top cone.
Welding speed should not be too high
The size of the welding speed is mainly determined by the thickness of the workpiece, and cooperate with the welding current, preheating temperature, to ensure the required melting depth and melting width. However, in high-speed automatic welding, the influence of welding speed on the gas protection effect should be considered, and it is not appropriate to use excessive welding speed. Because the welding speed is too large, the protective air flow is seriously backward, which may expose the tungsten extreme part, arc column and melting pool to the air, thus affecting the protection effect.
Do not use air flow arbitrarily
Argon arc welding welding protection gas is argon, purity is 99.99%. When the welding current is 40A to 160A, the argon flow rate is 8 to 10L/min, and when the current is 150A to 240A, the argon flow rate is 12 to 15L/min. Under certain conditions, there is an optimal matching range between gas flow and nozzle diameter. For manual argon arc welding, when the flow rate is 5-25L/min, the corresponding nozzle diameter is 5-20mm. Beyond this range, the airflow is too small or the nozzle diameter is too large, will make the airflow stiffness is poor, the ability to exclude the surrounding air is weak, and the protection effect is not good; If the airflow is too large or the nozzle diameter is too small, it will cause turbulence due to high airflow speed, which not only reduces the protection range, but also causes air involvement and reduces the protection effect.
Do not arbitrarily use the distance from the nozzle to the workpiece
The distance from the nozzle to the workpiece reflects the relative length and curvature of the electrode extension. When the electrode extension length is constant, the distance from the nozzle to the workpiece is changed, which not only changes the arc length, but also changes the state of the gas protection. If the distance between the nozzle and the workpiece is enlarged, the conical ground of the arc will be enlarged, and the gas protection effect will be greatly affected. However, if the distance is too close, it will not only affect the line of sight, but also easily make the tungsten wire contact with the molten pool, resulting in tungsten clamping defects. Tungsten pole protruding nozzle length, 4~5mm is preferable, in the fillet welding and other poor shielding place is 2~3mm, in the depth of the slot is 5~6mm, the distance between the top of the nozzle and the workpiece is 8-14mm, not more than 15mm.
Do not use the cleaning effect arbitrarily
The DC component and the cleaning effect of the cathode can be controlled by changing the ratio of positive and negative half wave power on time, but the appropriate minimum ratio should be selected according to the welding conditions, so that it can not only meet the needs of cleaning oxide film, but also obtain the maximum penetration depth and the minimum tungsten electrode loss. Although the ratio is too large, it can obtain a light cathode cleaning effect, but it will cause serious burning of tungsten electrode, and the welding pool will become shallow and wide, which is unfavorable to welding.
Aluminum and copper wires shall not be used in the hot wire welding process
The resistance heat generated in the front section of the welding wire by the additional power supply can heat the welding wire to a predetermined temperature, thus increasing the welding coating speed. However, for aluminum and copper, due to small resistivity, large heating power supply is required, resulting in too large arc magnetic bias blowing and melting uneven, so hot wire welding is not easy to use aluminum, copper wire.
Normal operation
In fact, the welding seam of argon arc welding is mainly: gas, heat input energy, welding machine stability.
- Look at the good and bad state of the welder, check the gas flow before welding, to ensure that the welder gas output is uniform, gas protection is stable and timely.
- Control the size of the welding heat input, match the welding current, voltage and welding speed according to the thickness of the welding material, adopt multi-layer and multi-pass welding, control the temperature between the welding layers, and prevent high temperature oxidation of the weld.
- After the welding machine is set up, the gas is pumped for 0.5-5 seconds, after the arc is closed, the welding gun does not leave immediately, and then blow for a while.
- Advance gas, before welding, the welder is set to advance gas function, set the time of 8 seconds, so that argon can protect the welding pass in advance.
- Check the purity of the gas.
- Check whether there is air leakage, plug the porcelain mouth, 5 seconds later let go, see if there is pressure.
- tungsten quality, tungsten quality may also lead to poor welding results, it is recommended to use large brands of tungsten welding operations.
No matter what kind of welding machine and plasma cutting machine you need, we can meet your needs. If you need advice beyond what is provided in this article, please contact our sales team. Our team of experts can help you make the right choice...