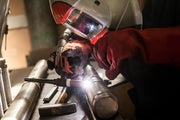
Understanding tungsten electrode
Tungsten electrode, it is made of tungsten electrode with high melting point, corrosion resistance, high density, good thermal and electrical conductivity materials. Tungsten electrode is widely used for welding in its properties. Its final color is different, you can tell the difference.
Tungsten electrode is used for TIG welding, which is a tungsten alloy bar made of 0.3-5% rare earth elements such as cerium, thorium, lanthanum, zirconium, yttrium, etc. in the tungsten matrix by powder metallurgy, and then processed by pressure, with a diameter from 0.25 to 6.4mm and a standard length from 75 to 600.
The most commonly used tungsten electrode specifications are diameter 1.0, 1.6, 2.4 and 3.2, the shape of the electrode end is an important factor for TIG, when using DC positive connection, tungsten extreme needs to be ground into a sharp shape, and its tip Angle changes with the application range, electrode diameter, and welding current, narrow joints require a small tip Angle, when welding very thin materials, It needs to be carried out with a small current, needle-like minimum electrode to stabilize the arc.
When using AC power to weld, aluminum magnesium welding, do not need to grind tungsten extreme, because the use of appropriate welding current, tungsten extreme will form half of the ball, if increased welding current, the electrical extreme will become bulb and may melt and pollute the weld pool.
In tungsten electrodes, more importantly, their final color is different, and the tungsten content is also different. When welding, choose the right tungsten electrode to make welding easier, it is important to obtain high quality welding.
Classification of tungsten electrode
Tungsten electrode can be divided into pure tungsten, thorium tungsten, cerium tungsten, lanthanum tungsten, etc. At present, the most in the market is thorium tungsten and cerium tungsten.
Pure tungsten (green) has a high melting and boiling point, is not easy to melt and play, burn, tip pollution is less, but the electron emission is poor, is not conducive to the stable combustion of the arc.
Thorium tungsten electrode (red) has strong electron emission ability, high allowable current density, and stable arc combustion, but thorium has certain radioactivity, and its use is limited to a certain extent.
Cerium tungsten electrode (gray) is a widely used electrode with low electron escape work, high chemical stability, large allowable current density and no radioactivity.
Zirconium tungsten electrode (white) can be selected for the base metal where electrode contamination must be prevented and under specific conditions. The tip of this electrode is easy to keep hemispherical, suitable for AC power welding.
The relationship between tungsten electrode diameter and welding
The choice of tungsten electrode diameter is mainly determined by the thickness of the weldment and the size of the welding current.
When the welding current exceeds the allowable value, the tungsten electrode will strongly heat and melt and volatilize, causing arc instability and welding defects such as clamping tungsten.
The following table lists the allowable current values for tungsten electrodes of different diameters:
Tungsten electrode diameter | Pure tungsten electrode | Thoriated-tungsten electrode | Cerium-tungsten electrode |
(mm) | Welding current range |
1.0 | 20A--60A | 15A--80A | 20A--80A |
1.6 | 40A--100A | 70A--150A | 50A--160A |
2.0 | 60A--150A | 100A--200A | 100A--200A |
2.5 | 130A--230A | 170A--250A | 170A--250A |
3.2 | 160A--310A | 225A--330A | 225A--330A |
4.0 | 275A--450A | 350A--480A | 350A--480A |
5.0 | 400A--625A | 500A--675A | 500A--675A |
When the diameter of the tungsten electrode is selected, if different power supply polarities are used, the allowable current of the tungsten electrode should also be changed accordingly.
The allowable current ranges of tungsten electrodes with different power supply polarities and different diameters are shown in the table below:
Tungsten electrode diameter | Welding current range |
(mm) | AC | DC direct connection | DC reverse connection |
1.0 | 15A--80A | / | 20A--60A |
1.6 | 70A--150A | 10A--20A | 60A--120A |
2.5 | 150A--250A | 15A--30A | 100A--180A |
3.2 | 250A--400A | 25A--40A | 170A--250A |
4.0 | 400A--500A | 40A--55A | 210A--320A |
5.0 | 500A--750A | 55A--80A | 300A--390A |
6.4 | 750A--1000A | 80A--125A | 350A--530A |
Tungsten electrode shape and application
During TIG welding, the shape of tungsten extreme part has a great influence on TIG. Reasonable tungsten electrode type and shape contribute to arc stability and improve welding performance.
1. Circular arc: suitable for AC power welding, but the arc is unstable when the direct current is connected.
2. Taper: Suitable for small current welding sheet and curved butt weld.
3. Cylindrical: suitable for welding aluminum, magnesium alloy. However, the direct current connection method is not available.
4. Flat bottom: suitable for direct current connection, concentrated arc, stable combustion, good weld formation.
Tungsten taper grinding, tip diameter should be appropriate, too large, arc instability; Too small, easy to melt. Generally, it is determined according to the size of the welding current. The length of the grinding is generally 3-5 times that of the tungsten pole, and the minimum diameter of the end should be 1/2 of the diameter of the tungsten pole.
At present, there are three main shapes of tungsten extremes in production applications: spherical, conical and conical with platform.
Spherical ends
Spherical ends are generally used in pure tungsten and zirconium tungsten electrodes for alternating current as well as traditional square-wave TIG welding. The first thing to note is that the spherical end is not ground out but produced after welding.
The arc is simply ignited under the recommended current conditions and, for a given electrode diameter, a spherical end will be formed at the end of the electrode. The diameter of the ball should not exceed 1.5 times the diameter of the tungsten pole. Too large end ball can reduce arc stability, and may fall off and contaminate the weld to form a clamp tungsten.
Conical or platform conical tungsten
Conical or platform conical tungsten (for pure tungsten, cerium tungsten, lanthanum tungsten and thorium tungsten) is suitable for AC and DC welding. Polishing the electrode into a cone shape can be easy to start the arc, produce a more concentrated arc, and thus have better welding performance. Choosing the right end shape and the right end Angle is crucial. The right choice depends on what you are trying to achieve.
When welding thin sheets (from 0.1mm to 1.0mm) with low current welding, it is recommended that the tungsten is extremely polished into a sharp cone. The conical end can be a more concentrated welding current and help prevent sheet distortion.
At higher current conditions, it is recommended to polish the electrical extremes into a cone with a platform. This end shape can prevent high current from melting the tungsten tip, resulting in contamination of the welding pool. Sharp conical ends are not recommended for use under high current conditions.
Tungsten extreme head grinding
In order to properly polish the tungsten electrode and prevent contamination, it is best to use a grinding wheel specially designed for grinding tungsten, which should have the hardness of grinding tungsten, and the axis of the tungsten pole should be in line with the tangent line of the direction of rotation of the grinding wheel to ensure that the grinding marks are longitudinal.
No matter what kind of welding machine and plasma cutting machine you need, we can meet your needs. If you need advice beyond what is provided in this article, please contact our sales team. Our team of experts can help you make the right choice...
🧐🧐🧐You might like the following:
1. Become a TIG Welding Pro: Mastering the Art of Aluminum Welding
2. Seven "minefields" to pay attention to when TIG welding
3. Why opt for TIG AC/DC welding?