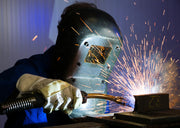
Welding is the strongest metal connection technology and the foundation of modern metal manufacturing. However, did you know that the earliest forms of welding date back to ancient times? Have you ever wondered who invented welding and what the original welding method looked like?
To satisfy your curiosity, we have decided to turn on the time machine and travel to the future to relive a fascinating journey through the history of welding, from the first signs of antiquity to the modern techniques we know and use today. So, close your eyes and we will travel back in time.
The origin of welding and ancient welding technology
1.1 Discovery and application of early welding technology
The historical evolution of welding technology is one of the important symbols of the progress of human civilization. Ancient Egyptians had mastered the technique of welding copper and gold as early as around 3000 BC, using simple heating and hammering methods to join pieces of metal together, and this primitive welding method was particularly common in ancient Egyptian jewelry making. According to archaeological findings, ancient Egyptian craftsmen were able to produce exquisite welding jewelry, which not only shows the early application of welding technology, but also reflects the exquisite mastery of the ancient Egyptian civilization. During the Roman period, welding technology was further developed, especially in the Iron Age, when blacksmiths welded iron sheets into various tools and weapons by heating and forging, and the inheritance and innovation of these techniques laid the foundation for later medieval welding technology.
1.2 Welding practices in Ancient Egypt and Rome
The welding practice in ancient Egypt and Rome is an indispensable part of the historical evolution of welding technology. In ancient Egypt, the application of welding technology dates back to around 3000 BC, when craftsmen used simple welding methods to join precious metals such as gold and silver to make fine jewelry and ornaments. According to archaeological findings, the ancient Egyptians had mastered the welding technology of copper and gold, and they combined different metal parts by heating the metal and taking advantage of the differences in the melting point of the metal itself. The use of this technology not only reflects the exquisite level of craftsmanship of ancient Egyptian craftsmen, but also demonstrates their deep understanding of material properties.
During the Roman period, welding technology was further developed, especially in the field of metal processing. Roman blacksmiths used welding techniques to create complex iron tools and weapons, such as swords, armor, and locks. A notable feature of Roman welding techniques was the use of lead welding, which was widely used in Roman water pipe systems. The Romans built complex systems of aqueducts and Bridges, many of which required welding techniques to ensure the tightness and durability of the pipes. For example, in the Roman aqueduct system, lead welding was used to join the joints of pipes to prevent water leakage. The use of this welding technology not only reflects the Roman engineers' proficiency in welding technology, but also reflects their high attention to public works.
Ancient Egyptian and Roman welding practices, although technically primitive compared to modern welding techniques, laid the foundation for the subsequent development of welding techniques. These cases of ancient welding technology not only show the early exploration of human material processing technology, but also provide valuable historical data for us to understand the evolution of welding technology. As the experts of modern welding technology say: "Every weld is a witness to history." The welding practice in ancient Egypt and Rome is an indispensable chapter in the long history of welding technology.
The development of medieval welding technology
2.1 Inheritance and innovation of welding technology in the Middle Ages
In the Middle Ages, the inheritance and innovation of welding technology is an important chapter in the history of metal technology development. Medieval blacksmiths inherited the essence of ancient welding techniques and made many innovations on this basis. For example, they are starting to use more efficient welding methods such as forging welding, which fuses heated metal surfaces by hammering them. This technology not only improves the strength of welding, but also reduces the dependence on welding materials. Historians speculate that forging welding was already widespread in Europe in the 12th century, marking the transition from a simple patching process to more complex and elaborate metalworking.
The innovation of welding technology in the Middle Ages is not only reflected in welding methods, but also in the use of welding materials. Blacksmiths began to experiment with different alloys to suit different welding needs. For example, they found that adding small amounts of carbon significantly increased the hardness and strength of iron, leading to the development of early steel. The use of this material provides a more robust and durable welding object for later welding technologies. As Da Vinci said: "details determine success or failure", the medieval blacksmith's grasp of the details of the material laid a solid foundation for the progress of welding technology.
In addition, the inheritance and innovation of medieval welding technology is also reflected in the standardization of the process. With the rise of cities and guilds, the welding process began to have preliminary norms and standards. Through guilds, blacksmiths share knowledge and experience and promote the spread and improvement of welding techniques. The standardization of this process not only improves the quality of welding, but also lays a social foundation for the further development of welding technology. These innovations in medieval welding technology laid the foundation for the diversification and specialization of modern welding technology.
Industrial revolution and welding technology change
3.1 The demand for welding technology driven by the industrial revolution
The Industrial Revolution, which began in Britain at the end of the 18th century and then swept through Europe and North America, marked the transformation of human society from an agricultural civilization to an industrial civilization. During this period, mechanized production replaced manual labor, and the widespread application of steam engines promoted a leap in productivity. With the deepening of industrialization, the demand for metal structures is growing, and welding technology has ushered in unprecedented development opportunities. In this period, the demand for welding technology was mainly reflected in the construction of railways, shipbuilding and the construction of large industrial facilities. For example, the Liverpool-Manchester railway, which opened in 1830, required extensive welding work to lay its tracks. The application of welding technology not only improves the production efficiency, but also reduces the material cost, making it possible to manufacture large-scale metal structures. As Henry Ford, one of the pioneers of the Industrial Revolution, said, "Without standardization, there can be no mass production." The standardization and standardization of welding technology laid the foundation for the standardization of production during the industrial revolution and greatly promoted the industrialization process.
3.2 Emergence and development of early industrial welding technology
In the historical evolution of welding technology, the emergence and development of early industrial welding technology marked a major shift from manual workshops to mechanized production. In the mid-19th century, with the advancement of the Industrial Revolution, the demand for large-scale production gave birth to the innovation of welding technology. In 1881, Russian engineer Nikolai Benediktov invented arc welding, which greatly improved the efficiency and quality of welding. Arc welding uses an electric current to melt metal through an arc created between two electrodes. In 1890, American inventor Charles Martin Hall invented aluminum welding, which further broadened the application range of welding technology. The emergence of these technologies has not only promoted the change of industrial production methods, but also laid the foundation for the diversification and specialization of subsequent welding technology.
The breakthrough of welding technology in the century
4.1 Invention and improvement of stick welding and gas welding technology
The invention of arc welding technology marks the major transformation of welding technology from traditional manual skills to modern industrial applications. In 1881, Nikola Tesla demonstrated the arc lamp at the Columbia Exposition in the United States, which not only illuminated the exposition, but also laid the foundation for the development of arc welding technology. Subsequently, Nikolai Bergmann applied for a patent for arc welding in 1882, which marked the official birth of arc welding technology. Arc welding uses the high temperature generated by the electric arc to melt and bind metals together, which greatly increases the speed and efficiency of welding compared to earlier welding methods, while reducing the dependence on the skill of the welder. For example, in the late 19th century, arc welding technology was used in the construction of the Eiffel Tower, and its structural complexity and scale are difficult to imagine without arc welding technology.
The development of gas welding technology has also had a profound impact on the evolution of welding technology. Gas welding technology uses a mixture of combustible gas and oxygen combustion to produce a high temperature flame, thereby melting metal for welding. In the mid-19th century, with the discovery of acetylene gas and the invention of acetylene welding gun, gas welding technology has been rapidly developed. Acetylene gas welding became one of the important technologies in the welding field at that time because of its easy operation and low cost. At the beginning of the 20th century, gas welding technology was widely used in automobile manufacturing, pipeline installation and other industries, which greatly promoted the development of these industries. For example, when Henry Ford promoted the production of automobiles on the assembly line, the application of gas welding technology significantly improved the production efficiency and laid the technical foundation for the mass production of automobiles.
4.2 Application of welding technology in the First World War
In the smoke of the First World War, the application of welding technology marked its transformation from traditional technology to modern industrial technology. The demands of war greatly promoted the development of welding technology, especially in shipbuilding and the manufacture of weapons. According to statistics, during the war, the application of welding technology in ship manufacturing significantly improved production efficiency and shortened construction time. For example, the "H-class" destroyers built by the British during the war were built faster than any previous model, thanks in part to the use of welding technology.Welding technology not only speeds up the construction of ships, but also improves the strength and durability of the structure. As welding engineer and inventor August Robert Pearson put it, "Advances in welding technology have allowed us to build more powerful ships with less material and greater safety." In addition, welding technology has also played a key role in the manufacture of guns, tanks and other military equipment, providing solid technical support for the mechanization process of war.
Modernization and standardization of welding technology
5.1 Standardization process of welding technology
The standardization process of welding technology is an important milestone in the history of welding technology, which marks the transformation of welding from a technology to a science. With the advancement of the industrial revolution, the application of welding technology in the manufacturing industry is becoming more and more extensive, and the requirements for welding quality are becoming higher and higher. In order to ensure the safety and reliability of welding products, the standardization of welding technology has become an urgent need. In 1919, the American Welding Society (AWS) was established and began to develop welding standards, which marked the official start of welding technology standardization. The first standard developed by AWS is the specification for arc welding, which provides clear guidance for welding operations and ensures the consistency of welding quality. Subsequently, the International Organization for Standardization (ISO) also joined the ranks of standardization, promoting a unified global standard for welding technology. For example, the ISO 9606-1 series of standards, Qualification of welding personnel for Metal materials, provides an internationally recognized framework for the certification of the skills of welding personnel. Standardization not only improves the efficiency of welding operations, but also promotes the innovation and application of welding technology, laying a solid foundation for the modernization of welding technology.
5.2 The role of welding technology in World War II and post-war reconstruction
During the Second World War, the application of welding technology reached an unprecedented height and became a key support for the production of war machines. According to statistics, during the war, the American shipbuilding industry reduced the construction time of ships by about 40% through the use of welding technology. The efficiency and strength advantages of welding technology were fully demonstrated in the wartime construction of ships, tanks and aircraft. For example, during the construction of Liberty ships in the United States, the application of welding technology has reduced the construction time of individual ships from months to weeks. Welding technology not only increased the speed of production, but also enhanced the durability of the structure, which was essential for the rapid production and transportation of wartime materials.
During the post-war reconstruction period, welding technology continued to play an important role. In post-war Europe, many cities and infrastructure were destroyed, and welding technology played an important role in the rebuilding process. For example, welding technology is widely used in the reconstruction of Bridges, railways and building structures, which not only speeds up reconstruction, but also improves the safety and durability of the structure. The standardization process of welding technology was also strengthened during this period, with the establishment of the International Institute of Welding (IIW), which promoted the development of international standards for welding technology and laid the foundation for industrial development on a global scale.
The application of welding technology in the Second World War and post-war reconstruction not only reflects its importance in industrial production, but also shows its key role in social and economic development. As Henry Ford said, "Quality is the lifeblood of a business." The continuous improvement and application of welding technology has ensured the quality of industrial products during and after the war, providing a solid technical support for the recovery and growth of global industry.
Innovation and application of contemporary welding technology
6.1 The rise of laser welding and electron beam welding technology
With the evolution of welding technology, the rise of laser welding and electron beam welding technology marks a major technological revolution in the field of welding. Laser welding technology, the use of high energy density laser beam as a heat source, to achieve the rapid melting and solidification of materials, so as to achieve the purpose of welding. This technology began to develop in the 1960s, and by the 1980s, with the breakthrough of laser technology, laser welding began to be widely used in industrial production. For example, in the automotive industry, laser welding technology is used in the stitching of the body, which not only improves the welding speed, but also significantly improves the welding quality and accuracy. Electron beam welding, which uses a high-speed electron beam as a heat source in a high vacuum environment, was invented in the 1950s and is favored for its ability to weld thick, deeply fused materials. The emergence of these two welding technologies not only promotes the modernization and standardization of welding technology, but also provides new possibilities for precision manufacturing in the fields of aerospace, automotive and construction. As Einstein said, "Every great achievement in science is the accumulation of a series of small steps." The development of laser welding and electron beam welding technology is a clear proof of continuous exploration and innovation in the field of welding technology.
6.2 Application of welding technology in aerospace, automotive and construction fields
The application of welding technology in the space field is one of the cornerstones of human exploration of the universe. The International Space Station, for example, cannot be built and maintained without advanced welding technology. In space, welding is not only necessary to ensure structural integrity, but also to adapt to extreme temperature changes and vacuum environments. According to NASA research, the use of laser welding technology can significantly improve the strength and durability of spacecraft components, while reducing the use of materials. In the field of automobile manufacturing, welding technology also plays a crucial role. In modern automobile manufacturing, welding technology is widely used in the assembly of body structures to ensure the safety and durability of vehicles. For example, the laser welding technology used by Ford Motor Company not only improves production efficiency, but also makes the body lighter, which improves fuel efficiency. In the field of construction, the application of welding technology is also indispensable. Towering skyscrapers and complex bridge structures all require metal components to be firmly joined together by welding technology. Taking the famous Golden Gate Bridge as an example, a lot of welding technology was used during its construction to ensure the stability of the bridge in strong winds and sea breezes. The innovation and application of welding technology has not only promoted the development of these industries, but also continuously challenged the wisdom of engineers to develop more efficient, safe and environmentally friendly welding methods.
Future trends and challenges of welding technology
7.1 Development and application of environmental protection welding technology
With the enhancement of global awareness of environmental protection, the development of welding technology is also gradually tending to the direction of green and environmental protection. The impact of smoke, harmful gases and radiation generated during welding on the environment and operator health has prompted the industry to constantly seek innovative solutions. For example, the use of laser welding technology can not only reduce material consumption and improve welding accuracy, but also significantly reduce the emission of harmful substances. According to one study, laser welding can reduce harmful gas emissions by about 70% compared to traditional welding. In addition, electron beam welding technology is performed in a vacuum environment and produces almost no smoke and harmful gases, providing a cleaner welding option for high-precision fields such as aerospace. The development of environmentally friendly welding technology is not only in line with the global trend of sustainable development, but also brings economic benefits to companies, as Edison said: "The future belongs to those who can combine innovation with environmental responsibility."
7.2 Prospect of automation and intelligent welding technology
With the advent of the Industry 4.0 era, welding technology is experiencing unprecedented automation and intelligent changes. According to the International Institute of Welding (IIW), the share of automated and robotic welding in the global welding market is expected to grow to more than 30% by 2025. This growth reflects not only the increasing demand for efficient and high-quality welding in the manufacturing industry, but also the importance of welding technology in responding to rising labor costs and skills shortages. For example, in modern automobile manufacturing, welding robots can complete the welding work of the body with extremely high precision and repeatability, significantly improving production efficiency and safety. Intelligent welding technologies, such as the use of machine vision and artificial intelligence algorithms for weld inspection and quality control, are becoming the new standard in the industry. As Henry Ford said, "Quality is the norm, not the exception." Intelligent welding technology is the key tool to transform this concept into reality.
🧐🧐🧐You might like the following:
1. How does a gasless mig welder work? How to choose ?
2. Difference between TIG welding machine and MIG welding machine.
3. The Power of as Laser Welding: A Look into the Future of Manufacturing.